Knitted jean production process and equipment
A technology for knitting denim and production technology, which is applied in textile processing machine accessories, textiles and papermaking, and textile material processing, etc. It can solve the problems of large difference in yarn depth, low efficiency of winding, easy yarn breakage, etc., and achieve consistent tension , saving workers, and increasing output
- Summary
- Abstract
- Description
- Claims
- Application Information
AI Technical Summary
Problems solved by technology
Method used
Image
Examples
Embodiment Construction
[0029] Reference figure 1 , figure 2 As shown, the main process of a knitted denim production process is: 1) Warp: hang the number of cotton yarn frays on the warp frame according to the process requirements (for example, 520 frays, 500 frays per fray), set The required production length (such as 30,000 meters) is composed of a single piece of warp yarn, which is wound on the warp beam; 2) Piece dyeing: the above single piece of warp yarn is placed on the unwinding frame of the sheet multi-head winder one by one, ( For example: a 30-head winder has 30 single pieces) After the warp beams are in place, pull out the respective yarn ends, separate the layers with nylon thread, and then all merge into the dyeing vat, then press dry, and then pass the exposed The wind performs oxidation and reduction, so that the dyeing can be repeated 10 times continuously, and the number of dyeing depends on the process requirements (such as the color depth); 3) Drying: After dyeing, the yarn ente...
PUM
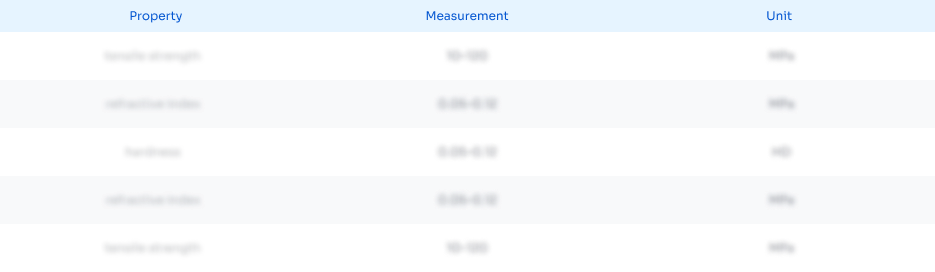
Abstract
Description
Claims
Application Information

- R&D Engineer
- R&D Manager
- IP Professional
- Industry Leading Data Capabilities
- Powerful AI technology
- Patent DNA Extraction
Browse by: Latest US Patents, China's latest patents, Technical Efficacy Thesaurus, Application Domain, Technology Topic, Popular Technical Reports.
© 2024 PatSnap. All rights reserved.Legal|Privacy policy|Modern Slavery Act Transparency Statement|Sitemap|About US| Contact US: help@patsnap.com