Double-solidification system fast-flowing underfill and preparation method thereof
An underfill, dual-curing technology, used in chemical instruments and methods, adhesives, epoxy resins, etc., can solve the problems of non-curing glue and poor compatibility, and achieve fast flow speed, low shrinkage, low odor effect
- Summary
- Abstract
- Description
- Claims
- Application Information
AI Technical Summary
Problems solved by technology
Method used
Image
Examples
Embodiment 1
[0036] Accurately weigh the following raw materials, 40 g of 3,4-epoxycyclohexylmethyl-3,4-epoxycyclohexyl carboxylate, bis(7-oxabicyclo[4.1.0]3-heptylmethyl) 40g of adipate and 0.5g of Super XC-7231 hexafluoroantimonate from King Company of the United States were put into the reaction kettle, mixed at 30°C for 30 minutes to dissolve into a homogeneous solution, and then 10g of acrylic epoxy resin, acrylic acid 5 g of butyl ester, 3 g of 1,4-butanediol, 1 g of β-(3,4-epoxycyclohexyl)ethyltrimethoxysilane, 0.3 g of benzoyl peroxide, and 0.2 g of carbon black. The temperature was controlled at 15° C., the degree of vacuum was -0.05 MPa, and the number of revolutions was 500 rpm, and the mixture was stirred and mixed in vacuum for 2 hours to obtain a uniform product.
Embodiment 2
[0038] Accurately weigh the following raw materials, 50g of bis(7-oxabicyclo[4.1.0]3-heptylmethyl) adipate, 20g of bisphenol A epoxy resin, and hexafluoroantimonate from the King Company of the United States. Put 3g of K-PURE CXC-1612 into the reaction kettle, mix at 35°C for 30 minutes to dissolve it into a homogeneous solution, then add 10g of acrylic epoxy resin, 8g of isooctyl acrylate, 6.5g of polycaprolactone polyol, γ-glycidyloxypropyltrimethoxysilane 2g, azobisisobutyronitrile 0.3g, carbon black 0.2g; control temperature at 15°C, vacuum degree -0.05MPa, rotation speed 1000 rpm, vacuum Mixing was stirred for 2 hours to obtain a homogeneous product.
[0039] Wherein, the structural formula of described bisphenol A type epoxy resin is:
[0040]
[0041] n is a mixture of compounds consisting of 0, 1, 2-18, and 19.
Embodiment 3
[0043] Accurately weigh the following raw materials, bis(7-oxabicyclo[4.1.0]3-heptylmethyl)adipate 30g, hexafluoroantimonate is K-PURE CXC-1612 1g input from King Company of the United States In the reaction kettle, mix at 30°C for 30 minutes to dissolve it into a uniform solution, then add 15g of acrylic epoxy resin, 30g of lauryl methacrylate, 20g of polyester polyol, 3g of γ-mercaptopropyltrimethoxysilane, 0.5 g of di-tert-butyl peroxide and 0.5 g of carbon black; the temperature was controlled at 15°C, the degree of vacuum was -0.07 MPa, the number of revolutions was 700 rpm, and the mixture was stirred and mixed in vacuum for 2 hours to obtain a uniform product.
PUM
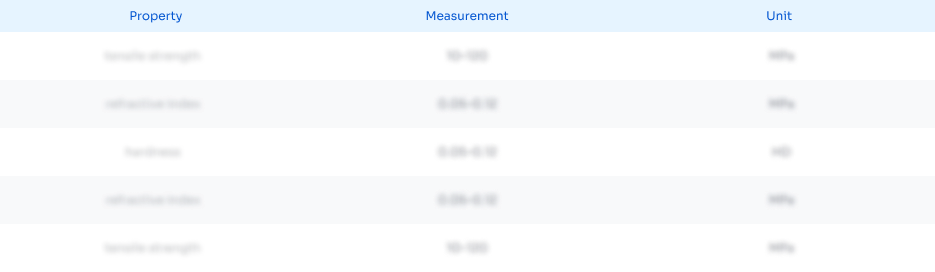
Abstract
Description
Claims
Application Information

- R&D
- Intellectual Property
- Life Sciences
- Materials
- Tech Scout
- Unparalleled Data Quality
- Higher Quality Content
- 60% Fewer Hallucinations
Browse by: Latest US Patents, China's latest patents, Technical Efficacy Thesaurus, Application Domain, Technology Topic, Popular Technical Reports.
© 2025 PatSnap. All rights reserved.Legal|Privacy policy|Modern Slavery Act Transparency Statement|Sitemap|About US| Contact US: help@patsnap.com