Method for manufacturing structural timber by sheet lamination of fast growing wood
A production method and technology for structural materials, which are applied to flat products, wood processing appliances, household components, etc., to achieve the effects of shortening hot pressing time, good shape stability of products, and low cost
- Summary
- Abstract
- Description
- Claims
- Application Information
AI Technical Summary
Problems solved by technology
Method used
Image
Examples
Embodiment 1
[0013] The small-diameter fast-growing poplar, fir, eucalyptus or masson pine raw material section is first processed into a 1.5-4.0mm thick veneer by a rotary cutting machine, and the veneer is dried naturally or artificially to a moisture content of 2%-10%. After coating, such as: PF, phenolic resin for double-sided coating of veneer, the amount of coating is 300g / m 2 ~440g / m 2 Finally, it is paved into slabs by machinery or supplemented by manual work. After the slabs are aged, they are finally sent to a combined hot press machine with a side steam spraying mechanism. In the hot press, the slab is compressed first, and then steamed laterally. The steam pressure is 0.3-0.9MPa, and the steaming time is 5-25s. Suction, absorb the condensed water vapor in the slab, and finally enter the ordinary pressing stage, so as to produce LVL structural materials with a thickness of 20-200mm or more, and the hot-pressing time is only 10-20s / mm, which is only the traditional hot-pressing ...
Embodiment 2
[0015] Small-diameter fast-growing poplar, fir, eucalyptus or masson pine raw materials, first cut into large shavings by a flaking machine, and then dry the shavings to a moisture content of 2% to 8% and apply adhesives, such as: MUF, MUF sizing amount 8% ~ After 12%, then realize the orientation structure of the slab with the help of a specific paving mechanism, and finally send it into a combined hot press machine with a side steam spraying mechanism. In the hot press, the slab is compressed first, and then steamed laterally. The steam pressure is 0.3-0.9MPa, and the steaming time is 5-25s. Suction, absorbing the condensed water vapor generated in the slab, and finally entering the stage of high-pressure and low-pressure ordinary pressing, so as to produce OSB structural materials with a thickness of 25-40mm or more, and the hot-pressing time is only 5-12s / mm, Only 1 / 5 to 1 / 12 of traditional hot pressing.
Embodiment 3
[0017] Small-diameter fast-growing poplar, Chinese fir, eucalyptus, masson pine and other raw material segments are first cut into strip-shaped shavings by a flaker, or the shredded veneers produced by the above-mentioned tree species in plywood rotary cutting are broken into single pieces of a certain length and width. Slats, then the shavings or veneer strips are dried to a moisture content of 2% to 8%, and then an adhesive such as: MDI is applied, after the amount of glue is 3% to 8%, and then the directional structure of the slab is realized by means of a specific paving mechanism , and finally sent to a combined heat press with a side steaming mechanism. In the hot press, the slab is compressed first, and then steamed laterally. The steam pressure is 0.3-0.9MPa, and the steaming time is 5-25s. Suction, absorb the condensed water vapor in the slab, and finally enter the ordinary pressing stage, so as to produce PSL structural materials with a thickness of 20-60mm or more, ...
PUM
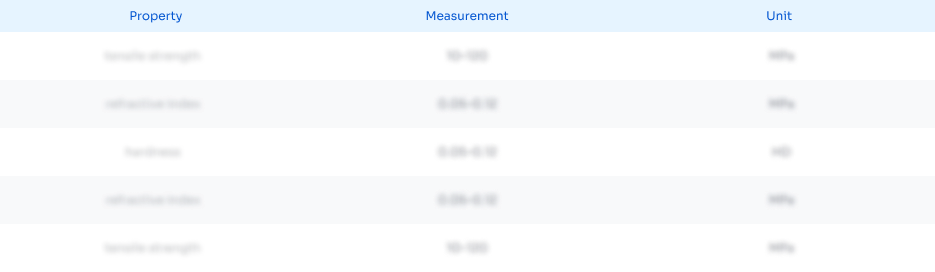
Abstract
Description
Claims
Application Information

- R&D
- Intellectual Property
- Life Sciences
- Materials
- Tech Scout
- Unparalleled Data Quality
- Higher Quality Content
- 60% Fewer Hallucinations
Browse by: Latest US Patents, China's latest patents, Technical Efficacy Thesaurus, Application Domain, Technology Topic, Popular Technical Reports.
© 2025 PatSnap. All rights reserved.Legal|Privacy policy|Modern Slavery Act Transparency Statement|Sitemap|About US| Contact US: help@patsnap.com