Method for preparing low-leaching-rate water-swellable rubbers
A technology of water-swellable rubber and dissolution loss rate, applied in the field of functional materials, can solve the problems of complex compatibilizer synthesis process, low dissolution rate of water-swellable rubber, and high equipment requirements, achieving good water retention performance and low equipment requirements. , the preparation method is simple
- Summary
- Abstract
- Description
- Claims
- Application Information
AI Technical Summary
Problems solved by technology
Method used
Image
Examples
Embodiment 1
[0024] Embodiment 1 superabsorbent resin preparation
[0025] Preparation of superabsorbent resin: prepare mixed monomers according to 60 parts by weight of methacrylic acid and 40 parts by weight of acrylamide, add 0.8 parts by weight of crosslinking agent N-N'-methylenebisacrylamide and 0.6 parts by weight of initiator K 2 S 2 o 8 , mixed and dissolved to obtain mixed solution A. In a certain reaction vessel, add 300 parts by weight of cyclohexane and 20 parts by weight of dispersant Span80, stir and heat up to 70-80°C, add the mixed solution A dropwise, after the dropwise addition, react at constant temperature for 5-6 hours, cool, and The reaction product was poured into a beaker filled with methanol, stirred to fully precipitate the reaction product, filtered with suction, washed several times with methanol, and dried in a vacuum box to obtain super absorbent resin A;
Embodiment 2
[0026] Embodiment 2 superabsorbent resin preparation
[0027] Preparation of superabsorbent resin: prepare mixed monomers according to 40 parts by weight of acrylic acid, 30 parts by weight of 2-acrylamide-2-methylpropanesulfonic acid and 30 parts by weight of acrylamide, and add 1.2 parts by weight of crosslinking agent N-N'-sub- Methylbisacrylamide and 0.6 parts by weight of initiator K 2 S 2 o 8 , mixed and dissolved to obtain mixed solution B. In a certain reaction vessel, add 500 parts by weight of cyclohexane and 30 parts by weight of dispersant Span80, stir and heat up to 70-80°C, add the mixed solution B dropwise, after the dropwise addition, react at constant temperature for 5-6 hours, cool, and Pour the reaction product into a beaker filled with methanol, stir to fully precipitate the reaction product, filter it with suction, wash it several times with methanol, and dry it in a vacuum box to obtain superabsorbent resin B;
Embodiment 3
[0028] Embodiment 3 superabsorbent resin preparation
[0029] Preparation of superabsorbent resin: prepare mixed monomers according to 80 parts by weight of 2-acrylamide-2-methylpropanesulfonic acid methacrylic acid and 20 parts by weight of acrylamide, and add 1.5 parts by weight of crosslinking agent N-N'-methylene Bisacrylamide and 0.4 parts by weight of initiator K 2 S 2 o 8, mixed and dissolved to obtain mixed solution C. In a certain reaction vessel, add 200 parts by weight of cyclohexane and 20 parts by weight of dispersant Span80, stir and heat up to 70-80°C, add the mixed solution C dropwise, after the dropwise addition, react at constant temperature for 5-6 hours, cool, and The reaction product was poured into a beaker filled with methanol, stirred to fully precipitate the reaction product, filtered with suction, washed several times with methanol, and dried in a vacuum box to obtain super absorbent resin C;
PUM
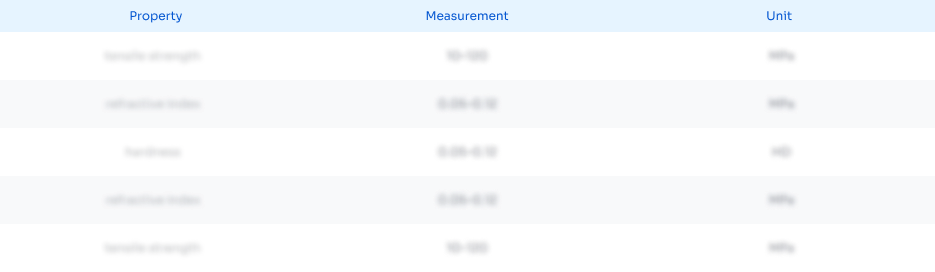
Abstract
Description
Claims
Application Information

- R&D
- Intellectual Property
- Life Sciences
- Materials
- Tech Scout
- Unparalleled Data Quality
- Higher Quality Content
- 60% Fewer Hallucinations
Browse by: Latest US Patents, China's latest patents, Technical Efficacy Thesaurus, Application Domain, Technology Topic, Popular Technical Reports.
© 2025 PatSnap. All rights reserved.Legal|Privacy policy|Modern Slavery Act Transparency Statement|Sitemap|About US| Contact US: help@patsnap.com