Preparation method of high-gravity spherical cobalt carbonate
A technology of cobalt carbonate and high specific gravity, applied in the direction of cobalt carbonate, etc., can solve problems such as unfavorable production efficiency, excessive particle growth, unfavorable product stability, etc., and achieve the effects of uniform and controllable particle size, short reaction time and large specific gravity.
- Summary
- Abstract
- Description
- Claims
- Application Information
AI Technical Summary
Problems solved by technology
Method used
Image
Examples
Embodiment 1
[0023] 1). Prepare cobalt sulfate aqueous solution and ammonium bicarbonate aqueous solution, wherein the cobalt concentration of cobalt sulfate aqueous solution is 30g / L, and the ammonium bicarbonate aqueous solution concentration is 200g / L. The prepared solutions were transferred to the elevated tank respectively, and the cobalt sulfate aqueous solution was preheated and kept at 40°C.
[0024] 2). Precipitation: Add 500ml of deionized water into the 10L reactor, raise the temperature to 60±5°C, and add the cobalt sulfate aqueous solution into the reactor at a slow speed and then quickly at a stirring speed of 800 rpm. Ammonium bicarbonate aqueous solution was added dropwise, the pH value of the reaction solution was controlled between 7.0 and 7.5, and the total volume of the reaction solution was increased to 7.5 L within 3 hours. Concrete feed process is: first feed at a slow speed until the total volume of the reaction solution reaches 2.5L, and the feed rate of the cobalt...
Embodiment 2
[0028] 1). Prepare cobalt sulfate aqueous solution and ammonium bicarbonate aqueous solution, wherein cobalt sulfate aqueous solution cobalt concentration is 50g / L, and ammonium bicarbonate aqueous solution concentration is 200g / L. The prepared solutions were transferred to the elevated tank respectively, and the cobalt sulfate aqueous solution was preheated and kept at 50°C.
[0029] 2). Precipitation: Add 500ml of deionized water into the 10L reactor, raise the temperature to 70±5°C, and under the condition of stirring speed of 1000 rpm, add the cobalt sulfate aqueous solution into the reactor slowly and then quickly, and at the same time Ammonium bicarbonate aqueous solution was added dropwise, the pH value of the reaction solution was controlled between 7.0 and 7.5, and the total volume of the reaction solution was increased to 7.5 L within 2 hours. Concrete feed process is: first feed at a slow speed until the total volume of the reaction solution reaches 3.5L, and the fe...
Embodiment 3
[0033] 1). Prepare cobalt sulfate aqueous solution and ammonium bicarbonate aqueous solution, wherein cobalt sulfate aqueous solution cobalt concentration is 50g / L, and ammonium bicarbonate aqueous solution concentration is 200g / L. The prepared solutions were transferred to the elevated tank respectively, and the cobalt sulfate aqueous solution was preheated and kept at 50°C.
[0034] 2). Precipitation: Add 500ml of deionized water into the 10L reactor, raise the temperature to 80±5°C, and under the condition of stirring speed of 1200 rpm, add the cobalt sulfate aqueous solution into the reactor slowly and then quickly, and at the same time Ammonium bicarbonate aqueous solution was added dropwise, the pH value of the reaction solution was controlled between 7.0 and 7.5, and the total volume of the reaction solution was increased to 7.5 L within 1 hour. Concrete feed process is: first feed at a slow speed until the total volume of the reaction solution reaches 4.5L, and the fee...
PUM
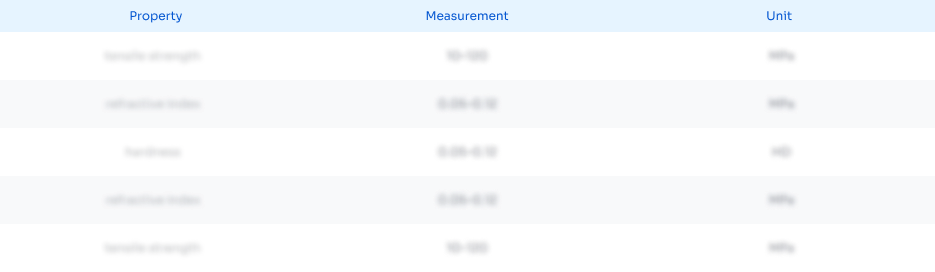
Abstract
Description
Claims
Application Information

- Generate Ideas
- Intellectual Property
- Life Sciences
- Materials
- Tech Scout
- Unparalleled Data Quality
- Higher Quality Content
- 60% Fewer Hallucinations
Browse by: Latest US Patents, China's latest patents, Technical Efficacy Thesaurus, Application Domain, Technology Topic, Popular Technical Reports.
© 2025 PatSnap. All rights reserved.Legal|Privacy policy|Modern Slavery Act Transparency Statement|Sitemap|About US| Contact US: help@patsnap.com