Sulfur-resisting and nitrogen-removed oxide compound metallic oxide SCR (Selective Catalytic Reduction) catalyst and preparation method thereof
A technology of SCR catalyst and nitrogen oxides, which is applied in the field of heterogeneous catalyst preparation, can solve the problems of increasing energy consumption and operating costs, and achieve the advantages of sulfur resistance performance, low temperature performance and simple preparation
- Summary
- Abstract
- Description
- Claims
- Application Information
AI Technical Summary
Problems solved by technology
Method used
Examples
Embodiment 1
[0027] (1) Dissolve cobalt nitrate, chromium nitrate and manganese nitrate with a metal molar ratio of 0.5:4:6 into 2mol / L citric acid solution at a ratio of 1:1 to citric acid molar ratio, and let stand for 1 hour Afterwards, obtain cobalt nitrate citric acid solution, chromium nitrate citric acid solution and manganese nitrate citric acid solution respectively;
[0028] (2) Mix cobalt nitrate citric acid solution, chromium nitrate citric acid solution and manganese nitrate citric acid solution at 5mL min -1 The total flow rate of the mixture was evenly added dropwise to the beaker and kept stirring continuously, and continued to stir for 2 hours after the dropwise addition to obtain a mixed solution;
[0029] (3) The mixed solution was dried in an oven at 150°C for 15 hours, and then calcined in a muffle furnace at a temperature of 650°C for 350 minutes;
[0030] (4) After the calcined product is pressed into tablets under a pressure of 6Kpa, it is ground into particles thr...
Embodiment 2
[0035] (1) Cobalt nitrate, chromium nitrate and manganese nitrate with a metal molar ratio of 2:5:5 were dissolved in 3mol / L citric acid solution at a ratio of 1:1.5 to citric acid molar ratio, and left to stand for 3 hours Afterwards, obtain cobalt nitrate citric acid solution, chromium nitrate citric acid solution and manganese nitrate citric acid solution respectively;
[0036] (2) Mix cobalt nitrate citric acid solution, chromium nitrate citric acid solution and manganese nitrate citric acid solution at 10mL min -1 The total flow rate is evenly added dropwise to the beaker and kept stirring continuously, after the dropwise addition, continue to stir for 0.5 hours to obtain a mixed solution;
[0037] (3) The mixed solution was dried in an oven at 90°C for 8 hours, and then calcined in a muffle furnace at a temperature of 600°C for 100 minutes;
[0038] (4) After the calcined product is pressed into tablets under a pressure of 15Kpa, it is ground into particles through a 60-m...
Embodiment 3
[0043] (1) Cobalt nitrate, chromium nitrate and manganese acetate with a metal molar ratio of 2:3:7 are dissolved in 2mol / L citric acid solution in a ratio of 1:2 to citric acid molar ratio, and left to stand for 2 hours Afterwards, obtain cobalt nitrate citric acid solution, chromium nitrate citric acid solution and manganese acetate citric acid solution respectively;
[0044] (2) Mix cobalt nitrate citric acid solution, chromium nitrate citric acid solution and manganese acetate citric acid solution at 8mL·min -1 The total flow rate is evenly added dropwise to the beaker and kept stirring continuously, after the dropwise addition, continue to stir for 3 hours to obtain a mixed solution;
[0045] (3) The mixed solution was dried in an oven at 130°C for 15 hours, and then calcined in a muffle furnace at a temperature of 700°C for 200 minutes;
[0046] (4) After the calcined product is pressed into tablets under a pressure of 8Kpa, it is ground into particles through an 80-mes...
PUM
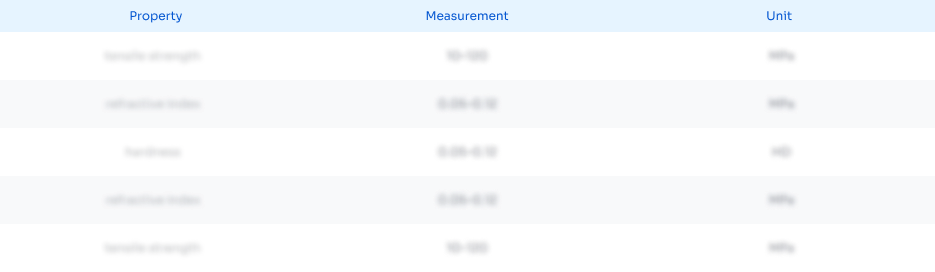
Abstract
Description
Claims
Application Information

- R&D
- Intellectual Property
- Life Sciences
- Materials
- Tech Scout
- Unparalleled Data Quality
- Higher Quality Content
- 60% Fewer Hallucinations
Browse by: Latest US Patents, China's latest patents, Technical Efficacy Thesaurus, Application Domain, Technology Topic, Popular Technical Reports.
© 2025 PatSnap. All rights reserved.Legal|Privacy policy|Modern Slavery Act Transparency Statement|Sitemap|About US| Contact US: help@patsnap.com