Grinding tool and grinding method for reheating main valve seat of steam turbine
A technology for reheating main valve and grinding tools, applied in grinding tools, grinding devices, grinding machine tools, etc., can solve the problems of large grinding tool loss, difficulty in manufacturing sand tiles, and difficulty in grinding.
- Summary
- Abstract
- Description
- Claims
- Application Information
AI Technical Summary
Problems solved by technology
Method used
Image
Examples
Embodiment Construction
[0017] Preferred embodiments of the present invention will be described in detail below in conjunction with the accompanying drawings.
[0018] Such as figure 1 As shown, the steam turbine reheating main steam valve seat includes a cylinder body 1, the bottom of the cylinder body 1 forms a conical valve port 2, and the surface of the conical valve port 2 is the grinding surface to be ground. The grinding tool for steam turbine reheating main steam valve seat includes a screw 3, the top of the screw 3 is provided with a handle 4, the bottom of the screw 3 is provided with a conical grinding tool 5, and the conical grinding tool 5 and the screw 3 are connected by a flat key 6 is fixedly connected, and the conical lapping tool 5 is adapted to the conical valve port 2. The tapered grinding tool 5 can be made of materials such as cast iron, copper, aluminum or hardwood. The screw rod 3 passes through the guide flange 8, the screw rod 3 and the guide flange 8 are slidingly connect...
PUM
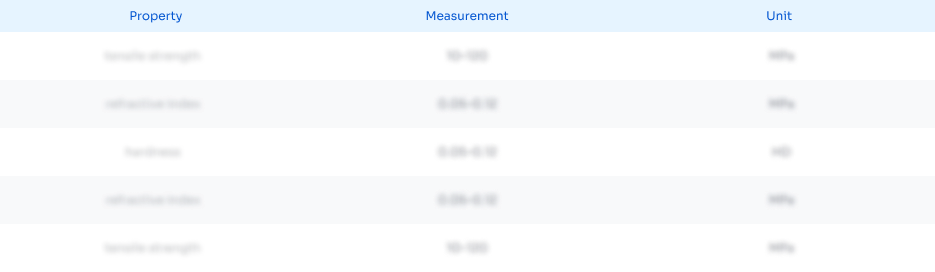
Abstract
Description
Claims
Application Information

- Generate Ideas
- Intellectual Property
- Life Sciences
- Materials
- Tech Scout
- Unparalleled Data Quality
- Higher Quality Content
- 60% Fewer Hallucinations
Browse by: Latest US Patents, China's latest patents, Technical Efficacy Thesaurus, Application Domain, Technology Topic, Popular Technical Reports.
© 2025 PatSnap. All rights reserved.Legal|Privacy policy|Modern Slavery Act Transparency Statement|Sitemap|About US| Contact US: help@patsnap.com