Method for manufacturing light-emitting diode (LED) structure
A technology of light-emitting diodes and diodes, applied in electrical components, circuits, semiconductor devices, etc., can solve problems such as emission wavelength drift, chip temperature rise, and affect chip luminous efficiency, and achieve the effect of improving lumen efficiency
- Summary
- Abstract
- Description
- Claims
- Application Information
AI Technical Summary
Problems solved by technology
Method used
Image
Examples
Embodiment Construction
[0026] The method for manufacturing the light emitting diode structure of the present invention will be further described in detail below with reference to the accompanying drawings.
[0027] Such as figure 1 As shown, the present invention is a method for manufacturing a method for manufacturing a light-emitting diode structure, characterized in that the method for manufacturing a method for manufacturing a light-emitting diode structure includes the following steps:
[0028] 1) The cured and packaged blue light emitting diode chip and the corresponding lead structure are prepared, and the blue light emitting diode chip is electrically connected and fixed to the wires in the lead structure;
[0029] 2) Apply transparent epoxy resin on the blue light-emitting diode chip that has been cured, packaged and electrically connected to the lead structure. The epoxy resin does not contain phosphor powder, and then cured. Thin, the thinner the coating thickness, the better the LED lum...
PUM
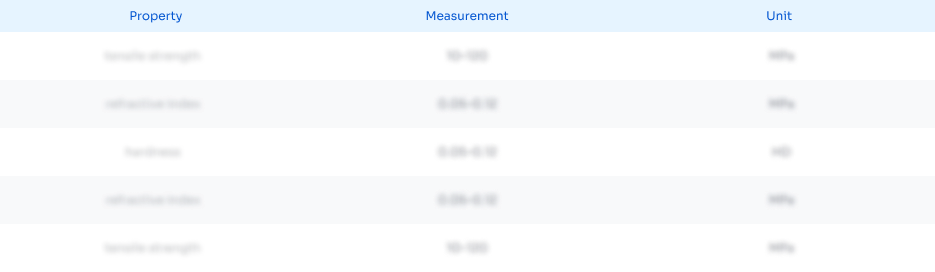
Abstract
Description
Claims
Application Information

- R&D Engineer
- R&D Manager
- IP Professional
- Industry Leading Data Capabilities
- Powerful AI technology
- Patent DNA Extraction
Browse by: Latest US Patents, China's latest patents, Technical Efficacy Thesaurus, Application Domain, Technology Topic, Popular Technical Reports.
© 2024 PatSnap. All rights reserved.Legal|Privacy policy|Modern Slavery Act Transparency Statement|Sitemap|About US| Contact US: help@patsnap.com