Preparation method of UV protection polyester cotton shell fabric
An anti-ultraviolet and anti-ultraviolet technology, applied in the field of polyester-cotton fabrics, can solve the problems affecting the air permeability and hand feeling of the fabric, and achieve the effects of safe, non-toxic, high-efficiency anti-ultraviolet rays, high tear and color fastness, and soft hand feeling.
- Summary
- Abstract
- Description
- Claims
- Application Information
AI Technical Summary
Problems solved by technology
Method used
Examples
Embodiment 1
[0023] (1) With 240dtex144f polyester high elastic yarn as warp yarn, the cotton-polyester blended yarn of 60% cotton 40% polyester is weft yarn, and is woven into base cloth with the plain weave method of 1 / 1 through water-jet loom;
[0024] The machine speed of the water jet loom is 500 rpm; the hydraulic pressure is 4 atmospheres.
[0025] (2) base cloth is carried out degreasing treatment;
[0026] At a temperature of 100°C and a pressure of 300kPa, the base cloth prepared in step (1) is continuously refined for 8 hours with the deoiling treatment liquid, and the deoiling treatment liquid includes (by weight) 2% Decontamination spiritual powder, 1.5% hydrogen peroxide, 25% liquid alkali and 70-75% pure water; the weight ratio of soda ash and water in the liquid alkali is 0.5:1.
[0027] (3) Under the condition that the temperature is 200° C. and the pressure is 500 kPa, the base cloth obtained in step (2) is continuously dyed in a 12-hour cycle; the dyeing bath ratio is 5...
Embodiment 2
[0032] (1) With 240dtex144f polyester high elastic yarn as warp yarn, the cotton-polyester blended yarn of 60% cotton 40% polyester is weft yarn, and is woven into base cloth with the plain weave method of 1 / 1 through water-jet loom;
[0033] The machine speed of the water-jet loom is 530 rpm; the hydraulic pressure is 4.5 atmospheres.
[0034] (2) base cloth is carried out degreasing treatment;
[0035] At a temperature of 110°C and a pressure of 350kPa, the base cloth prepared in step (1) is continuously refined for 8 hours with the oil-removing treatment liquid, and the oil-removal treatment liquid includes (by weight) 2% Decontamination spiritual powder, 1.5% hydrogen peroxide, 25% liquid alkali and 70-75% pure water; the weight ratio of soda ash and water in the liquid alkali is 0.5:1.
[0036] (3) Under the condition that the temperature is 210° C. and the pressure is 550 kPa, the base cloth obtained in step (2) is continuously colored for 12 hours in a cycle; the dyein...
Embodiment 3
[0041] (1) With 240dtex144f polyester high elastic yarn as warp yarn, the cotton-polyester blended yarn of 60% cotton 40% polyester is weft yarn, and is woven into base cloth with the plain weave method of 1 / 1 through water-jet loom;
[0042] The machine speed of the water jet loom is 550 rpm; the hydraulic pressure is 5 atmospheres.
[0043] (2) base cloth is carried out degreasing treatment;
[0044] At a temperature of 120°C and a pressure of 400kPa, the base cloth prepared in step (1) is continuously refined for 8 hours with the oil-removing treatment liquid, which includes (by weight) 2% Decontamination spiritual powder, 1.5% hydrogen peroxide, 25% liquid alkali and 70-75% pure water; the weight ratio of soda ash and water in the liquid alkali is 0.75:1.
[0045] (3) Under the condition that the temperature is 220° C. and the pressure is 600 kPa, the base cloth obtained in step (2) is continuously colored for 12 hours in a cycle; the dyeing bath ratio is 10:100.
[0046...
PUM
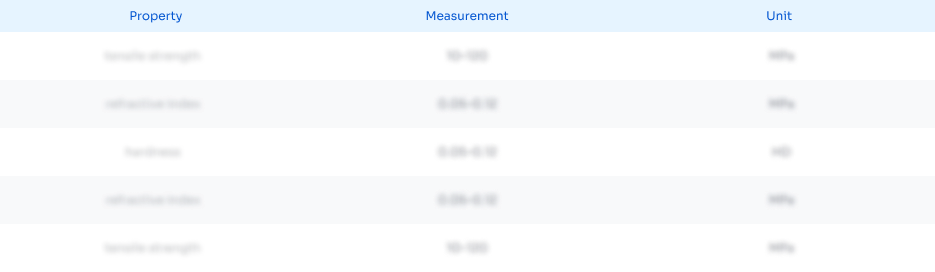
Abstract
Description
Claims
Application Information

- R&D
- Intellectual Property
- Life Sciences
- Materials
- Tech Scout
- Unparalleled Data Quality
- Higher Quality Content
- 60% Fewer Hallucinations
Browse by: Latest US Patents, China's latest patents, Technical Efficacy Thesaurus, Application Domain, Technology Topic, Popular Technical Reports.
© 2025 PatSnap. All rights reserved.Legal|Privacy policy|Modern Slavery Act Transparency Statement|Sitemap|About US| Contact US: help@patsnap.com