Industrial boiler water treatment method
An industrial boiler and water treatment technology, which is applied in the directions of water/sewage multi-stage treatment, water/sludge/sewage treatment, magnetic field/electric field water/sewage treatment, etc. It can solve the problem of scaling soda water, affecting heat transfer and normal circulation of soda water , Shorten the life of the boiler and other problems, to prevent the deposition of inorganic scale, improve the effect of scale and corrosion inhibition, and improve the effect of heat exchange efficiency
- Summary
- Abstract
- Description
- Claims
- Application Information
AI Technical Summary
Problems solved by technology
Method used
Image
Examples
Embodiment 1
[0031] The boiler feed water is tap water, and its main composition is shown in Table 1.
[0032] Table 1 Main components of tap water used in experiments
[0033]
[0034] Boiler operating conditions: 194°C, 1.25MPa.
[0035] Scale and corrosion inhibition methods:
[0036] Combined use of physical water treatment and chemical scale and corrosion inhibitors, of which (1) the physical water processor consists of two parts: a DC pulse generator and an external electromagnetic field sensor. The main technical indicators: use AC 220V, 50Hz power supply, working voltage 15V, output The power is 120W, the frequency conversion range is 20Hz~75KHz, and the carrier frequency is 1MHz. (2) The chemical scale and corrosion inhibitors are 2mg / L hydroxyethylene diphosphonic acid, 25mg / L molybdate and 10mg / L sodium sulfite.
[0037] Scale and corrosion inhibition effect: Through hanging test, the scale inhibition rate is 93.4%, and the corrosion inhibition rate is 88.2%.
Embodiment 2
[0039] The boiler feed water is tap water, and its main composition is shown in Table 1.
[0040] Boiler operating conditions: 194°C, 1.25MPa.
[0041] Scale and corrosion inhibition methods:
[0042] Combined use of physical water treatment and chemical scale and corrosion inhibitors, of which (1) the physical water processor consists of two parts: a DC pulse generator and an external electromagnetic field sensor. The main technical indicators: use AC 220V, 50Hz power supply, working voltage 15V, output The power is 120W, the frequency conversion range is 20Hz~75KHz, and the carrier frequency is 1MHz. (2) The chemical scale and corrosion inhibitors are 4mg / L hydroxyethylene diphosphonic acid, 50mg / L molybdate, and 20mg / L sodium sulfite.
[0043] Scale and corrosion inhibition effect: Through hanging test, the scale inhibition rate is 96.9%, and the corrosion inhibition rate is 95.7%.
Embodiment 3
[0045] The boiler feed water is tap water, and its main composition is shown in Table 1.
[0046] Boiler operating conditions: 194°C, 1.25MPa.
[0047] Scale and corrosion inhibition methods:
[0048] Combined use of physical water treatment and chemical scale and corrosion inhibitors, of which (1) the physical water processor consists of two parts: a DC pulse generator and an external electromagnetic field sensor. The main technical indicators: use AC 220V, 50Hz power supply, working voltage 15V, output The power is 120W, the frequency conversion range is 20Hz~75KHz, and the carrier frequency is 1MHz. (2) The chemical scale and corrosion inhibitors are 0.2mg / L hydroxyethylene diphosphonic acid, 5mg / L molybdate, and 1mg / L sodium sulfite.
[0049] Scale and corrosion inhibition effect: Through hanging test, the scale inhibition rate is 71.3%, and the corrosion inhibition rate is 78.5%.
PUM
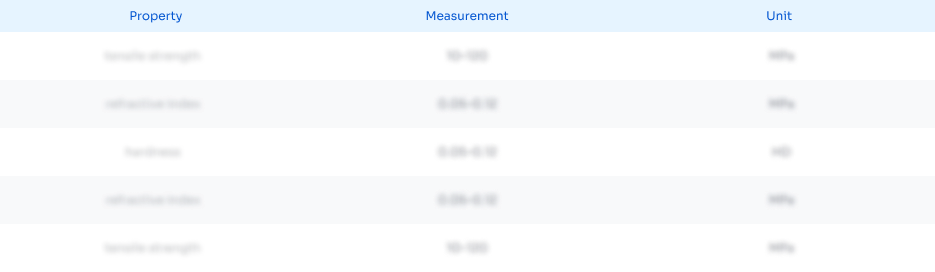
Abstract
Description
Claims
Application Information

- Generate Ideas
- Intellectual Property
- Life Sciences
- Materials
- Tech Scout
- Unparalleled Data Quality
- Higher Quality Content
- 60% Fewer Hallucinations
Browse by: Latest US Patents, China's latest patents, Technical Efficacy Thesaurus, Application Domain, Technology Topic, Popular Technical Reports.
© 2025 PatSnap. All rights reserved.Legal|Privacy policy|Modern Slavery Act Transparency Statement|Sitemap|About US| Contact US: help@patsnap.com