Powerful breathable fiber mid-sole material and manufacturing method
A technology of breathable fiber and manufacturing method, which is applied in the direction of shoe sole, fiber type, fiber treatment, etc., can solve the problems that cannot meet the requirements of high-performance end products, and achieve the effect of excellent strength, low product cost and simple operation
- Summary
- Abstract
- Description
- Claims
- Application Information
AI Technical Summary
Problems solved by technology
Method used
Examples
Embodiment 1
[0015] 1. Evenly mix 50 parts of 7.0D, 40 parts of 15D polyester staple fiber, 5 parts of high-strength elastic yarn, 2 parts of polypropylene fiber, and 2 parts of ES fiber. After opening, the original fiber block is loosened into fibers Or fiber bundles, the fiber bundles after loosening are further mixed through a mixer.
[0016] 2. Transfer the mixed fibers to the carding machine in a regular and quantitative manner, and the carding machine combs the opened fiber bundles into single fiber filaments and then forms a web. After the fiber web is overlapped, the weight per unit area of the cotton web will be obtained.
[0017] 3. Process the fiber web into an acupuncture material with a certain mechanical strength, thickness and grammage by acupuncture reinforcement.
[0018] 4. After finishing the acupuncture materials, the finishing solution is: 20 parts of modified nitrile emulsion (H), 20 parts of modified nitrile emulsion (S), 75 parts of carboxylated styrene-butadiene...
Embodiment 2
[0024] 1. Evenly mix 40 parts of 7.0D, 45 parts of 15D polyester staple fiber with 10 parts of high-strength elastic yarn, 2 parts of polypropylene fiber, and 2 parts of ES fiber, and the original fiber block will be loosened into fibers after opening Or fiber bundles, the fiber bundles after loosening are further mixed through a mixer.
[0025] 2. Transfer the mixed fibers to the carding machine in a regular and quantitative manner, and the carding machine combs the opened fiber bundles into single fiber filaments and then forms a web. After the fiber web is overlapped, the weight per unit area of the cotton web will be obtained.
[0026] 3. Process the fiber web into an acupuncture material with a certain mechanical strength, thickness and grammage by acupuncture reinforcement.
[0027] 4. After finishing the acupuncture materials, the finishing solution is: 15 parts of modified nitrile emulsion (H), 10 parts of modified nitrile emulsion (S), 100 parts of carboxylated sty...
Embodiment 3
[0033] 1. Evenly mix 40 parts of 7.0D, 55 parts of 15D polyester staple fiber, 2 parts of high-strength elastic yarn, 1 part of polypropylene fiber, and 2 parts of ES fiber, and the original fiber block will be loosened into fibers after opening Or fiber bundles, the fiber bundles after loosening are further mixed through a mixer.
[0034] 2. Transfer the mixed fibers to the carding machine in a regular and quantitative manner, and the carding machine combs the opened fiber bundles into single fiber filaments and then forms a web. After the fiber web is overlapped, the weight per unit area of the cotton web will be obtained.
[0035] 3. Process the fiber web into an acupuncture material with a certain mechanical strength, thickness and grammage by acupuncture reinforcement.
[0036] 4. After finishing the acupuncture material, the finishing solution is: 20 parts of modified nitrile emulsion (H), 50 parts of modified nitrile emulsion (S), 50 parts of carboxylated styrene-but...
PUM
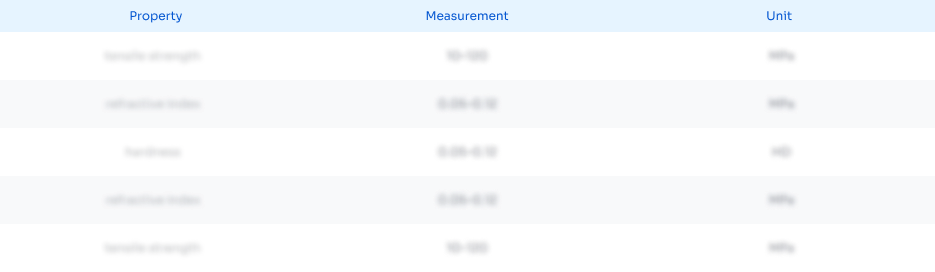
Abstract
Description
Claims
Application Information

- R&D Engineer
- R&D Manager
- IP Professional
- Industry Leading Data Capabilities
- Powerful AI technology
- Patent DNA Extraction
Browse by: Latest US Patents, China's latest patents, Technical Efficacy Thesaurus, Application Domain, Technology Topic, Popular Technical Reports.
© 2024 PatSnap. All rights reserved.Legal|Privacy policy|Modern Slavery Act Transparency Statement|Sitemap|About US| Contact US: help@patsnap.com