Thermoplastic chlorinated polyethylene cable material and preparation method thereof
A chlorinated polyethylene and production method technology, applied in the field of cable materials, can solve the problems of not meeting the long-term development plan of cables, high scrap rate, unsafe hidden dangers, etc., and achieve good ozone aging resistance and low content of toxic substances , the effect of great technological progress
- Summary
- Abstract
- Description
- Claims
- Application Information
AI Technical Summary
Problems solved by technology
Method used
Examples
Embodiment 1
[0029] The thermoplastic chlorinated polyethylene cable material of this embodiment packs the following components by weight:
[0030] Chlorinated polyethylene: CPE135A, 50 parts; CPE135B, 50 parts;
[0031] Reinforcing modifier: low-density polyethylene (LDPE), 20 parts; EVA 18-3,14-2,28-6,28-25 ,40 copies;
[0032] Plasticizer: dibutyl phthalate (DBP), 20 parts; 52# chlorinated paraffin (PCL-50), 15 parts;
[0033] Filling material: light calcium carbonate, 200 parts;
[0034] Dynamic crosslinking agent: vinyltrioxyethylene silane (A151), 0.8 parts; bis 25, 0.8 parts; 1-bis(tert-butyl peroxide)-3,5,5 trimethylcyclohexane, 0.8 parts;
[0035] Sulfurized acid absorber: light magnesium oxide, 15 parts;
[0036] Additives: triple salt, 1.5 parts; di-salt, 1.5 parts; barium stearate, 2 parts; zinc stearate, 2 parts; stearic acid, 1.5 parts; polyethylene wax, 1.5 parts;
[0037] Pigments: Lithor Red, Lithor Scarlet, 0.2 parts.
[0038]The preparation steps of this thermopla...
Embodiment 2
[0042] The thermoplastic chlorinated polyethylene cable material of this embodiment packs the following components by weight:
[0043] Chlorinated polyethylene: CPE135B, 100 parts;
[0044] Reinforcing modifier: polypropylene (PP), 20 parts; thermoplastic elastomer TPS, 50 parts;
[0045] Plasticizer: dibutyl phthalate (DBP), 15 parts; 52# chlorinated paraffin (PCL-50), 20 parts;
[0046] Filler: light calcium carbonate, 150 parts; light magnesium carbonate, 50 parts;
[0047] Dynamic crosslinking agent: vinyl trioxyethylene silane (A151), 1 part; 1-bis(tert-butyl peroxide)-3,5,5 trimethylcyclohexane, 1 part;
[0048] Sulfurized acid absorber: light magnesium oxide, 15 parts;
[0049] Additives: triple salt, 1.5 parts; di-salt, 1.5 parts; barium stearate, 2 parts; zinc stearate, 2 parts; stearic acid, 1.5 parts; polyethylene wax, 1.5 parts;
[0050] Pigment: titanium dioxide, 0.2 parts.
[0051] The preparation method of this embodiment product is the same as embodiment 1...
Embodiment 3
[0057] The thermoplastic chlorinated polyethylene cable material of this embodiment packs the following components by weight:
[0058] Chlorinated polyethylene: CPE135A, 100 parts;
[0059] Reinforcing modifier: low-density polyethylene (LDPE), 20 parts; polypropylene (PP), 20 parts;
[0060] Plasticizers: dibutyl phthalate (DBP), 35 parts; dioctyl adipate (DOA), 10 parts;
[0061] Filling material: light calcium carbonate, 240 parts;
[0062] Dynamic crosslinking agent: vinyl trioxyethylene silane (A151), 1 part; bis 25, 0.5 part; 1-di(tert-butyl peroxide)-3,5,5 trimethylcyclohexane, 0.5 copies;
[0063] Sulfurized acid absorber: light magnesium oxide, 10 parts; lead oxide, 5 parts;
[0064] Additives: triple salt, 1.5 parts; di-salt, 1.5 parts; barium stearate, 2 parts; zinc stearate, 2 parts; stearic acid, 1.5 parts; polyethylene wax, 1.5 parts;
[0065] Pigment: phthalocyanine blue, 0.2 parts.
[0066] The preparation method of the product of this embodiment is the s...
PUM
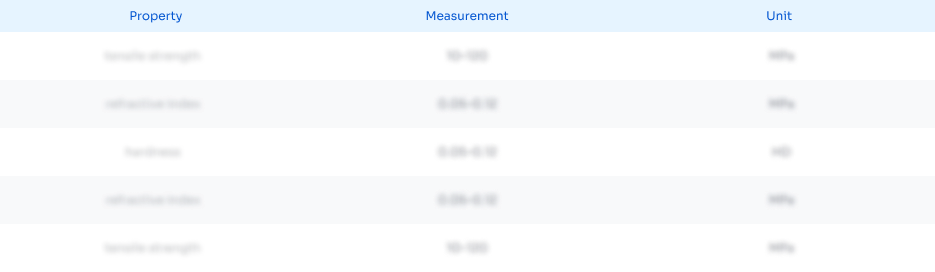
Abstract
Description
Claims
Application Information

- R&D
- Intellectual Property
- Life Sciences
- Materials
- Tech Scout
- Unparalleled Data Quality
- Higher Quality Content
- 60% Fewer Hallucinations
Browse by: Latest US Patents, China's latest patents, Technical Efficacy Thesaurus, Application Domain, Technology Topic, Popular Technical Reports.
© 2025 PatSnap. All rights reserved.Legal|Privacy policy|Modern Slavery Act Transparency Statement|Sitemap|About US| Contact US: help@patsnap.com