Engine mounting heat-resisting material and preparation method thereof
A technology of engine mounts and heat-resistant materials, applied in the field of modified rubber parts, can solve the problems of high heat resistance and durability of engine mounts, and achieve the effects of improving NVH performance, increasing vulcanization speed, and improving heat resistance
- Summary
- Abstract
- Description
- Claims
- Application Information
AI Technical Summary
Problems solved by technology
Method used
Image
Examples
Embodiment 1
[0028] Prepare according to the following recipe:
[0029] Standard natural rubber (SMR5#): 80 parts, butadiene rubber (BR9000): 20 parts, zinc oxide: 5 parts, stearic acid: 1 part, 2,2,4-trimethyl-1,2-dihydrogenation Quinoline polymer (antiaging agent RD): 1 part, N-isopropyl-N-phenyl-p-phenylenediamine (4010NA): 2 parts, compound paraffin (L5880): 3 parts, carbon black (N-774) : 35 parts, complex soap salt (NB76): 3 parts, precipitated white carbon black (175GR): 5 parts, silane coupling agent (Logsil 4C): 1 part, sulfur (S-80): 1 part, diethyl Zinc dithiocarbamate: 1 part; N-cyclohexyl-2-benzothiazole sulfenamide: 2 parts.
[0030] One-stage mixing: put standard natural rubber (SMR5#) and butadiene rubber (BR9000) in an internal mixer and knead for 25 seconds to mix the two rubbers evenly; then add zinc oxide, stearic acid, 2, 2, 4 - Trimethyl-1,2-dihydroquinoline polymer (antiaging agent RD), N-isopropyl-N-phenyl-p-phenylenediamine (4010NA), complex paraffin (L5880) and ...
PUM
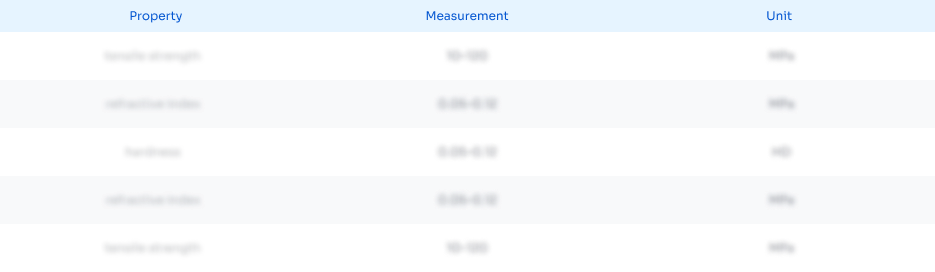
Abstract
Description
Claims
Application Information

- R&D
- Intellectual Property
- Life Sciences
- Materials
- Tech Scout
- Unparalleled Data Quality
- Higher Quality Content
- 60% Fewer Hallucinations
Browse by: Latest US Patents, China's latest patents, Technical Efficacy Thesaurus, Application Domain, Technology Topic, Popular Technical Reports.
© 2025 PatSnap. All rights reserved.Legal|Privacy policy|Modern Slavery Act Transparency Statement|Sitemap|About US| Contact US: help@patsnap.com