Technology for processing high strength large hexagon-headed bolt used for steel structure
A processing technology and high-strength technology, used in bolts, connecting components, manufacturing tools, etc., can solve the problems of reducing the degree of oxidation and decarburization on the surface of the workpiece, the impact of engineering quality, and delayed thread breakage, saving raw materials and high production efficiency. , The effect of improving the utilization rate of materials
- Summary
- Abstract
- Description
- Claims
- Application Information
AI Technical Summary
Problems solved by technology
Method used
Examples
Embodiment approach 1
[0027] The bolt specification of the present invention adopts 35CrMo when M27-M30, and 20MnTiB is used as the blank when the specification is M16-M24. Its processing method is: adopt less and no cutting processing, including three times of cold extrusion molding and one-time hot forging molding, that is The first cold extrusion forming is screw forming, the second cold extrusion forming is the thread section forming on the screw, the third cold extrusion forming is thread forming, and the hot forging forming is bolt riser forming.
[0028] Concrete processing step of the present invention is carried out as follows:
[0029] (1) Material preparation: choose 35CrMo or 20MnTiB as the blank, and remove the blank according to the specifications and sizes of the bolts.
[0030] (2) Hot forging header: Hot forging the bolt header at a temperature of 900°C in a high-frequency induction heater, the frequency of the high-frequency induction current is 20,000 Hz, and then cooled.
[003...
specific Embodiment approach 2
[0042] The bolt specification of the present invention adopts 35CrMo when M27-M30, and 20MnTiB is used as the blank when the specification is M16-M24. Its processing method is: adopt less and no cutting processing, including three times of cold extrusion molding and one-time hot forging molding, that is The first cold extrusion forming is screw forming, the second cold extrusion forming is the thread section forming on the screw, the third cold extrusion forming is thread forming, and the hot forging forming is bolt riser forming.
[0043] Concrete processing step of the present invention is carried out as follows:
[0044] (1) Material preparation: choose 35CrMo or 20MnTiB as the blank, and remove the blank according to the specifications and sizes of the bolts.
[0045] (2) Hot forging header: Hot forging the bolt header at a temperature of 1000°C in a high-frequency induction heater, the frequency of the high-frequency induction current is 50,000 Hz, and then cooled.
[00...
specific Embodiment approach 3
[0057] The bolt specification of the present invention adopts 35CrMo when M27-M30, and 20MnTiB is used as the blank when the specification is M16-M24. Its processing method is: adopt less and no cutting processing, including three times of cold extrusion molding and one-time hot forging molding, that is The first cold extrusion forming is screw forming, the second cold extrusion forming is the thread section forming on the screw, the third cold extrusion forming is thread forming, and the hot forging forming is bolt riser forming.
[0058] Concrete processing step of the present invention is carried out as follows:
[0059] (1) Material preparation: choose 35CrMo or 20MnTiB as the blank, and remove the blank according to the specifications and sizes of the bolts.
[0060] (2) Hot forging header: Hot forging the bolt header at a temperature of 950°C in a high-frequency induction heater, the frequency of the high-frequency induction current is 40,000 Hz, and then cooled.
[006...
PUM
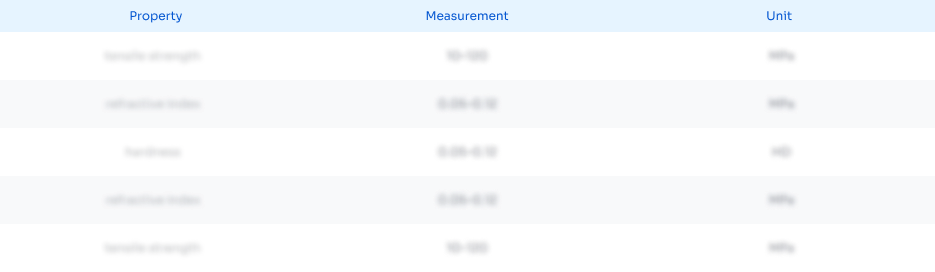
Abstract
Description
Claims
Application Information

- R&D Engineer
- R&D Manager
- IP Professional
- Industry Leading Data Capabilities
- Powerful AI technology
- Patent DNA Extraction
Browse by: Latest US Patents, China's latest patents, Technical Efficacy Thesaurus, Application Domain, Technology Topic, Popular Technical Reports.
© 2024 PatSnap. All rights reserved.Legal|Privacy policy|Modern Slavery Act Transparency Statement|Sitemap|About US| Contact US: help@patsnap.com