Method for producing high-content and high-optical purity butyl lactate with two-step method
A technology of butyl lactate and optical purity, applied in chemical instruments and methods, organic chemistry, chemical/physical processes, etc., can solve problems such as butyl lactate not mentioned
- Summary
- Abstract
- Description
- Claims
- Application Information
AI Technical Summary
Problems solved by technology
Method used
Examples
example 1
[0024]The raw material is purchased lactic acid with a content of 88%, and the raw material lactic acid is vacuum distilled by a falling film evaporator. The temperature of the material in the falling film evaporator is maintained at 60°C, and the vacuum degree is maintained at 8000Pa. The monomer content of the concentrated lactic acid is Above 99%. Transfer 500Kg of concentrated lactic acid into the polycondensation tank through a delivery pump, add zinc lactate as a catalyst at a weight ratio of zinc lactate to lactic acid of 5 / 10000, and raise the material from 80°C to 120°C within 2 hours. The vacuum degree is maintained at 5000Pa, and the whole reaction is carried out with stirring. The viscosity of the lactic acid oligomer is detected by an online viscometer. According to the relationship between viscosity and molecular weight, determine whether its molecular weight is between 1000 and 2500. Inside, the oligomeric lactic acid is transported into the depolymerization tan...
example 2
[0026] 500Kg of concentrated lactic acid is transported into the polycondensation tank through a delivery pump, and zinc oxide is added as a catalyst according to the weight ratio of zinc oxide and lactic acid as 10 / 10000. Within 2.5 hours, the material is raised from 80°C to 120°C. The vacuum degree is maintained at 4000Pa, and the whole reaction is carried out with stirring. The viscosity of the lactic acid oligomer is detected by an online viscometer. According to the relationship between viscosity and molecular weight, its molecular weight is determined to be 1600. The oligomeric lactic acid is transported into the depolymerization tank, and zinc oxide is added as a catalyst according to the weight ratio of zinc oxide to lactic acid of 10 / 10000. The whole reaction is carried out under the condition of stirring, and the material is rapidly heated to 185°C, vacuum The temperature is maintained at 1500Pa. After the lactide vapor obtained continuously is condensed, it is enrich...
example 3
[0028] 500Kg of lactic acid purchased with a content of 95% is transported into the polycondensation tank through a delivery pump, and a mixed catalyst is added in a ratio of 10 / 10000 by weight ratio of the catalyst to lactic acid. The mixed catalyst is zinc oxide, tin oxide and butyl titanate according to A mixture with a weight ratio of 1:1:1. Within 2.5 hours, the material was raised from 80°C to 120°C, the vacuum degree was maintained at 5000Pa ~ 4000Pa, the whole reaction was carried out with stirring, and the viscosity of the lactic acid oligomer was detected by an online viscometer. relationship, confirm that its molecular weight is 2000, and the polycondensation is completed, the oligomeric lactic acid is transported into the depolymerization kettle through the height difference and vacuum pressure difference, and the mixed catalyst is added in a ratio of 8 / 10000 according to the weight ratio of the catalyst to the lactic acid, and the mixed catalyst is oxidation A mix...
PUM
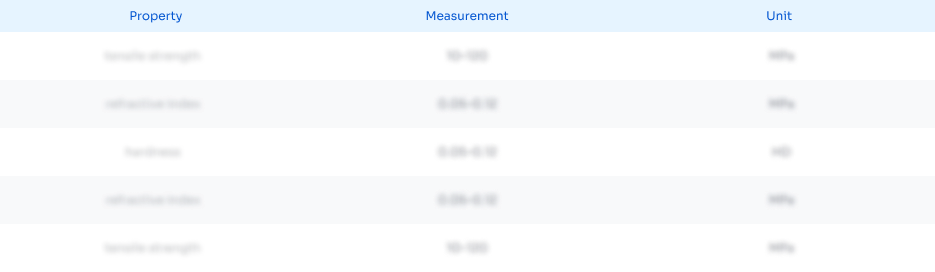
Abstract
Description
Claims
Application Information

- R&D
- Intellectual Property
- Life Sciences
- Materials
- Tech Scout
- Unparalleled Data Quality
- Higher Quality Content
- 60% Fewer Hallucinations
Browse by: Latest US Patents, China's latest patents, Technical Efficacy Thesaurus, Application Domain, Technology Topic, Popular Technical Reports.
© 2025 PatSnap. All rights reserved.Legal|Privacy policy|Modern Slavery Act Transparency Statement|Sitemap|About US| Contact US: help@patsnap.com