Method for preparing ZnO nanorod/microrod crystals with accurate controllable growth position on substrate
A microrod and substrate technology, applied in ion implantation plating, coating, metal material coating process, etc., can solve the problems of unsuitable electron beam lithography, high cost, etc.
- Summary
- Abstract
- Description
- Claims
- Application Information
AI Technical Summary
Problems solved by technology
Method used
Image
Examples
Embodiment approach 1
[0021] Step 1, the polycrystalline Si substrate is ultrasonically cleaned for 15 minutes with toluene, acetone, ethanol and deionized water in sequence, after cleaning, it is blown dry with nitrogen and quickly put into the vacuum chamber of the magnetron sputtering equipment. The vacuum degree of the vacuum chamber before sputtering starts is 3×10 -3 Pa, a metal Zn target with a purity of 99.99% is used for sputtering.
[0022] Step two, when starting the magnetron sputtering, the vacuum chamber is fed with Ar and O with a purity of 99.5%. 2 The mixed gas, the sputtering power is 100W, Ar and O 2 The flow ratio is 10sccm: 10sccm. During the sample preparation process, the substrate temperature was 340° C., and after sputtering for 1 hour, an 80 nm-thick ZnO thin film seed layer was deposited on the substrate.
[0023] Step 3, annealing the grown ZnO thin film at 500° C. for 2 hours in air.
[0024] Step 4, on the ZnO film seed layer treated in Step 3, use a coater to spin...
Embodiment approach 2
[0032] In step 1, the single crystal Si substrate is ultrasonically cleaned for 15 minutes with toluene, acetone, ethanol and deionized water in sequence. After cleaning, it is blown dry with nitrogen and quickly put into the vacuum chamber of the magnetron sputtering equipment. The vacuum degree of the vacuum chamber before sputtering starts is 3×10 -3 Pa, a metal Zn target with a purity of 99.99% is used for sputtering.
[0033] Step two, when starting the magnetron sputtering, the vacuum chamber is fed with Ar and O with a purity of 99%. 2 The mixed gas, the sputtering power is 200W, Ar and O 2 The flow ratio is 15 sccm: 15 sccm. During the sample preparation process, the substrate temperature was 300° C., and after sputtering for 1 hour, a 120 nm-thick ZnO thin film seed layer was deposited on the substrate.
[0034] Step 3, annealing the grown ZnO thin film at 400° C. for 2 hours in air.
[0035] Step 4, on the ZnO thin film seed layer treated in Step 3, use a coater ...
Embodiment approach 3
[0043] Step 1: Use toluene, acetone, ethanol, and deionized water to ultrasonically clean the amorphous substrates such as glass, ceramics, copper plates, or aluminum plates for 15 minutes in sequence. After cleaning, dry them with nitrogen and quickly put them into the magnetron sputtering equipment. in a vacuum chamber. The vacuum degree of the vacuum chamber before sputtering starts is 3×10 -3 Pa, a metal Zn target with a purity of 99.99% is used for sputtering.
[0044] Step two, when starting the magnetron sputtering, the vacuum chamber is fed with Ar and O with a purity of 99.1%. 2 The mixed gas, the sputtering power is 300W, Ar and O 2 The flow ratio is 20sccm:20sccm. During the sample preparation process, the substrate temperature was 25° C., and after sputtering for 1 h, a 200 nm-thick ZnO thin film seed layer was deposited on the substrate.
[0045] Step 3, annealing the grown ZnO thin film at 400° C. for 2 hours in air.
[0046] Step 4, on the ZnO thin film see...
PUM
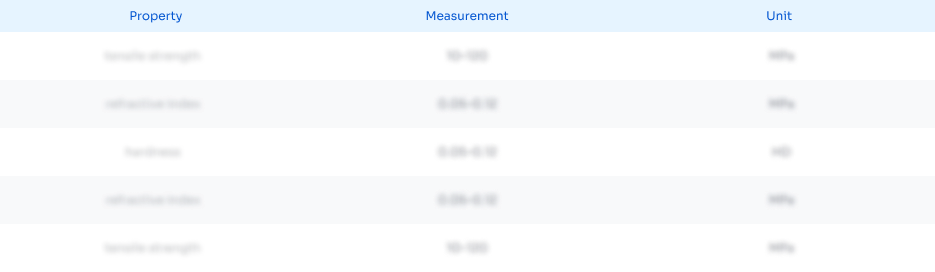
Abstract
Description
Claims
Application Information

- R&D Engineer
- R&D Manager
- IP Professional
- Industry Leading Data Capabilities
- Powerful AI technology
- Patent DNA Extraction
Browse by: Latest US Patents, China's latest patents, Technical Efficacy Thesaurus, Application Domain, Technology Topic, Popular Technical Reports.
© 2024 PatSnap. All rights reserved.Legal|Privacy policy|Modern Slavery Act Transparency Statement|Sitemap|About US| Contact US: help@patsnap.com