Recyclable desulfurizer and preparation method thereof and regeneration method
A desulfurizer and waste agent technology, which is applied in the fields of sulfur preparation/purification, catalyst regeneration/reactivation, separation method, etc. The effect of easy regeneration and high sulfur capacity
- Summary
- Abstract
- Description
- Claims
- Application Information
AI Technical Summary
Problems solved by technology
Method used
Examples
Embodiment 1
[0025] Preparation of Materials Containing Amorphous Iron Oxyhydroxide:
[0026] Mix 2560g of ferrous sulfate heptahydrate powder with 1030g of sodium hydroxide evenly, wherein the molar ratio of iron to hydroxide is 1:2.8; put the above mixed material into a kneader, control the reaction temperature to 40-50°C and knead 3h, so as to complete the solid-phase reaction between the above-mentioned reactants, and then put the above-mentioned reaction product in the air to dry, so as to facilitate the full completion of the above-mentioned reaction. Stir the dried material with water first, and wash repeatedly until the obtained filtrate has no sulfate radicals (usually tested with barium chloride), and then use a centrifuge to filter the above washing liquid. Dry the above-mentioned washed and filtered solid at a drying temperature of 80° C. and a drying time of 3 hours to obtain material A containing amorphous iron oxyhydroxide. In material A, 97.0 wt% of amorphous hydroxyl Iron...
Embodiment 2
[0033] Preparation of Materials Containing Amorphous Iron Oxyhydroxide:
[0034] Mix 2560g of ferrous sulfate heptahydrate powder with 883g of sodium hydroxide evenly, wherein the molar ratio of iron to hydroxide is 1:2.4; put the above mixed material into a kneader, control the reaction temperature to 80°C and knead for 0.5 h, thereby completing the solid-phase reaction between the above-mentioned reactants, and then putting the above-mentioned reaction product in the air to dry. Stir the dried material with water first, and wash repeatedly until the obtained filtrate has no sulfate radicals (usually tested with barium chloride), and then use a centrifuge to filter the above washing liquid. The above-mentioned washed and filtered solid was naturally dried at a drying temperature of -5° C. and a drying time of 10 h to obtain a material B containing amorphous iron oxyhydroxide. In this material B, it contains 95.8wt% amorphous iron oxyhydroxide, and the balance is sodium sulfa...
Embodiment 3
[0040] Preparation of Materials Containing Amorphous Iron Oxyhydroxide:
[0041] Mix 4320g of ferrous nitrate hexahydrate powder and 1680g of potassium hydroxide evenly, wherein the molar ratio of iron to hydroxide is 1:2.0; put the above mixture into a kneader, control the reaction temperature to 60-70°C and knead 1.0h, thereby completing the solid-phase reaction between the above-mentioned reactants, and then putting the above-mentioned reaction product in the air to dry. Add water to the dried material, stir it, and wash it repeatedly until the obtained filtrate is free of potassium ions (detected by flame photometry), and then use a centrifuge to filter the washing solution. Naturally dry the above-mentioned washed and filtered solid at a drying temperature of 45° C. and a drying time of 3 hours to obtain a material C containing amorphous iron oxyhydroxide. In material C, 96.1 wt % of amorphous hydroxyl Iron oxide, the balance is potassium nitrate and water, and its sulfu...
PUM
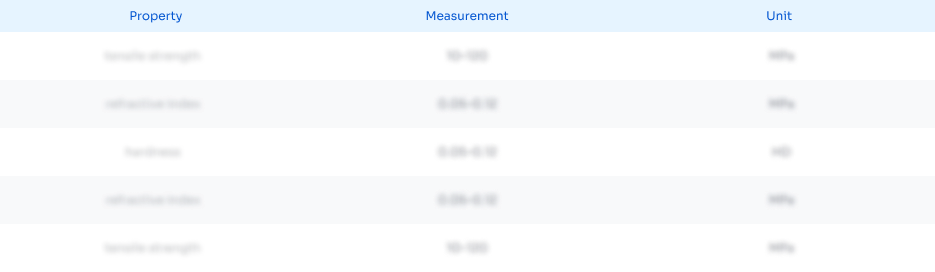
Abstract
Description
Claims
Application Information

- R&D
- Intellectual Property
- Life Sciences
- Materials
- Tech Scout
- Unparalleled Data Quality
- Higher Quality Content
- 60% Fewer Hallucinations
Browse by: Latest US Patents, China's latest patents, Technical Efficacy Thesaurus, Application Domain, Technology Topic, Popular Technical Reports.
© 2025 PatSnap. All rights reserved.Legal|Privacy policy|Modern Slavery Act Transparency Statement|Sitemap|About US| Contact US: help@patsnap.com