Superfine cupper powder and preparation method thereof
A technology of ultra-fine copper powder and copper powder, applied in the direction of improving process efficiency, can solve the problems of easy mixing of impurities, low direct copper yield, coarse particle size, etc., to avoid the introduction of impurities, high recovery yield, Avoid the effect of oxidation
- Summary
- Abstract
- Description
- Claims
- Application Information
AI Technical Summary
Problems solved by technology
Method used
Image
Examples
Embodiment 1
[0037] A kind of superfine copper powder and preparation method thereof, technological process is as follows figure 1 As shown, it uses hydrometallurgy copper slag as raw material. It soaks 1000g of copper slag containing 45.38% copper in 10g / L sulfuric acid solution for 10min, filters and dries, and roasts at 400°C for 6h. After roasting, the copper The slag was leached under the condition of controlling the terminal acidity to be 20g / L to obtain 310g leaching slag, which contained 0.72% copper, and the leaching rate of copper was 99.08%. Purify the copper sulfate leaching solution with sodium hydroxide, adjust the pH value to 3.5, and take part of the purified solution to make about 1000 mL of copper sulfate solution with a copper content of 0.3 mol / L for use.
[0038] Under the condition of constant stirring, add sodium hydroxide to 1000mL0.3mol / L copper sulfate solution to adjust the pH value to 11, then add 14.8g glucose powder, control the reaction temperature to 60°C, a...
Embodiment 2
[0042] A kind of superfine copper powder and preparation method thereof, technological process is as follows figure 1 As shown, it uses hydrometallurgy copper slag as raw material. It soaks 1000g of copper slag containing 45.38% copper in 10g / L sulfuric acid solution for 20min, filters and dries, and roasts at 500°C for 5h. After roasting, the copper The slag was leached under the condition of controlling the terminal acidity to be 15g / L to obtain 308g leached slag, the slag contained 0.65% copper, and the leaching rate of copper was 99.27%. Purify the leaching solution with sodium hydroxide, adjust the pH value to 3.5, and take part of the purified solution to make about 1000 mL of copper sulfate solution containing 0.3 mol / L copper for use.
[0043] Under the condition of constant stirring, add sodium hydroxide to 1000mL0.3mol / L copper sulfate solution to adjust the pH to 12, then add 14.8g glucose powder, control the reaction temperature to 70°C, and the reaction time to 13...
Embodiment 3
[0047] A kind of superfine copper powder and preparation method thereof, technological process is as follows figure 1 As shown, it uses hydrometallurgy copper slag as raw material. It soaks 1000g of copper slag containing 45.38% copper in 8g / L sulfuric acid solution for 30min, filters and dries, and roasts at 550°C for 4.5h. The copper slag was leached under the condition of controlling the terminal acidity to be 15g / L to obtain 311g leaching slag, the slag contained 0.62% copper, and the leaching rate of copper was 99.36%. Purify the leaching solution with sodium hydroxide, adjust the pH value to 4.0, and take part of the purified solution to make about 1000 mL of copper sulfate solution containing 0.5 mol / L copper for use.
[0048] Under the condition of constant stirring, add sodium hydroxide to 1000mL0.5mol / L copper sulfate solution to adjust the pH to 13, then add 24.8g glucose powder, control the reaction temperature to 80°C, and the reaction time to 100min to obtain cup...
PUM
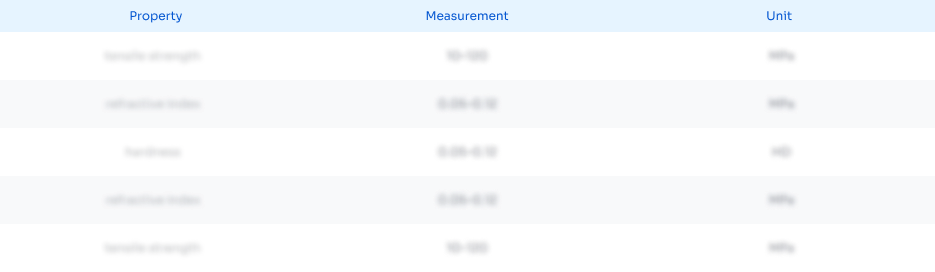
Abstract
Description
Claims
Application Information

- R&D
- Intellectual Property
- Life Sciences
- Materials
- Tech Scout
- Unparalleled Data Quality
- Higher Quality Content
- 60% Fewer Hallucinations
Browse by: Latest US Patents, China's latest patents, Technical Efficacy Thesaurus, Application Domain, Technology Topic, Popular Technical Reports.
© 2025 PatSnap. All rights reserved.Legal|Privacy policy|Modern Slavery Act Transparency Statement|Sitemap|About US| Contact US: help@patsnap.com