Processing method for increasing stamping formability of 6111 aluminium alloy automobile sheet
A technology of stamping formability and processing method, which is applied in the field of processing to improve the formability of 6111 aluminum alloy automobile sheets, can solve the problems that the stamping formability of aluminum alloy automobile sheets cannot meet the requirements of stamping production, achieve considerable social and economic benefits, improve Stamping yield and the effect of reducing stamping costs
- Summary
- Abstract
- Description
- Claims
- Application Information
AI Technical Summary
Problems solved by technology
Method used
Image
Examples
Embodiment 1
[0011] The 6111 alloy slab ingot produced by semi-continuous casting is put into the circulating air furnace at room temperature, and the temperature is raised to 370°C for 3 hours, then the temperature is raised to 550°C for 24 hours, and the furnace is air-cooled. To start rolling, first roll 3 passes along the width direction of the slab, and then roll along the length direction of the slab to form a plate with a thickness of about 6 mm. After cutting the hot-rolled sheet to length, it is directly annealed at 420°C for 2 hours, and finally cold-rolled into a thin sheet with a thickness of 0.8 mm. The sheet was subjected to solution treatment at 550°C×7min in a salt-bath furnace, and then placed in a drying oven for pre-aging treatment at 170°C×5min within 1 minute, and then placed at room temperature for 2 weeks before tensile and cupping tests were performed. After the plate is pre-deformed by 2%, it is heated in a drying oven at 170°C×30min to simulate baking paint, and t...
Embodiment 2
[0013] The 6111 alloy flat ingot produced by semi-continuous casting is put into the circulating air furnace at room temperature, and the temperature is raised to 220°C for 10 hours, then heated to 550°C for 24 hours, then air-cooled after being cut and milled, and reheated to 445°C To start rolling, first roll 3 passes along the width direction of the slab, and then roll along the length direction of the slab to form a plate with a thickness of about 6 mm. After cutting the hot-rolled sheet to length, it is directly annealed at 430°C×1h, and finally cold-rolled into a thin sheet with a thickness of 1.0mm. The sheet was subjected to solution treatment in a salt bath furnace for 550°C×7min, then quenched at room temperature for 48h, then placed in a drying oven for pre-aging treatment at 200°C×6min, and then stretched and stretched after 2 weeks at room temperature. In the cupping test, the plate is pre-deformed by 2%, and then heated in a drying oven at 170°C×30min to simulate...
Embodiment 3
[0015] The 6111 alloy flat ingot produced by semi-continuous casting is put into the circulating air furnace at room temperature, and the temperature is raised to 300°C for 15 hours, and then the temperature is raised to 550°C for 24 hours, and the furnace is air-cooled. After cutting the head and milling, reheat to 440°C To start rolling, first roll 3 passes along the width direction of the slab, and then roll along the length direction of the slab to form a plate with a thickness of about 6 mm. After cutting the hot-rolled plate to length, it is directly annealed at 420°C for 1.5h, and finally cold-rolled into a thin plate with a thickness of 0.8mm. The sheet was solution treated in a salt bath furnace for 550°C×7min, quenched, and then parked at room temperature for 12 hours, then placed in a drying oven for pre-aging treatment at 165°C×15min, and stretched after 2 weeks at room temperature. In the cupping test, the plate is pre-deformed by 2%, and then heated in a drying o...
PUM
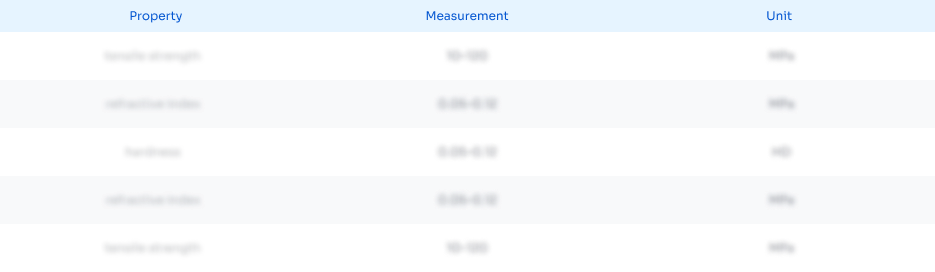
Abstract
Description
Claims
Application Information

- R&D
- Intellectual Property
- Life Sciences
- Materials
- Tech Scout
- Unparalleled Data Quality
- Higher Quality Content
- 60% Fewer Hallucinations
Browse by: Latest US Patents, China's latest patents, Technical Efficacy Thesaurus, Application Domain, Technology Topic, Popular Technical Reports.
© 2025 PatSnap. All rights reserved.Legal|Privacy policy|Modern Slavery Act Transparency Statement|Sitemap|About US| Contact US: help@patsnap.com