Recycled flue gas desulfurization and denitration method
A technology for desulfurization, denitrification and resource utilization, which is applied in the field of removal of NO and SO2 in flue gas and realization of resource utilization respectively, which can solve problems such as low fertilizer efficiency, difficulty in forming high value-added resource-based products, secondary pollution, etc.
- Summary
- Abstract
- Description
- Claims
- Application Information
AI Technical Summary
Problems solved by technology
Method used
Image
Examples
Embodiment 1
[0050] Flue gas condition: 15000Nm 3 / h,SO 2 Concentration 2000ppm (5714mg / Nm 3 ), NO concentration 460ppm (616mg / Nm 3 ), the temperature is 150°C.
[0051] Absorption liquid (poor liquid) composition: sodium sulfite 16.78%, sodium bisulfite 11.45%, antioxidant hydroquinone 0.03%, sodium sulfide 0.02%.
[0052] The flue gas enters the desulfurization tower (the desulfurization tower is a corrugated structured packing tower), and the lean liquid is sprayed into the tower from the upper part of the tower with a flow rate of 2t / h. After desulfurization, the composition of the rich liquid at the bottom of the desulfurization tower is: 8.69% sodium sulfite and 23.37% sodium bisulfite. SO in the flue gas exiting the top of the tower 2 The content is 190mg / Nm 3 , the desulfurization rate is 96.6%.
[0053] After the rich liquid is desorbed by the second-effect evaporator, SO 2 , to obtain liquid SO after condensation and compression 2 82.8kg / h. The solution after desorptio...
Embodiment 2
[0056] Flue gas condition: 54200Nm 3 / h,SO 2 Concentration 1560ppm (4457mg / Nm 3 ), NO concentration 650ppm (875mg / Nm 3 ), the temperature is 140°C.
[0057] The composition of the absorption liquid (poor liquid): 13.58% of sodium sulfite, 5.6% of sodium bisulfite, 0.01% of antioxidant methyl-p-phenylenediamine, and 0.03% of sodium dithionite.
[0058] The flue gas enters the desulfurization tower (desulphurization tower spray tower), and the lean liquid is sprayed into the tower from the upper part of the tower with a flow rate of 5.5t / h. After desulfurization, the composition of the rich liquid at the bottom of the desulfurization tower is: 5.6% sodium sulfite and 24.96% sodium bisulfite. SO in the flue gas exiting the top of the tower 2 The content is 89mg / Nm 3 , the desulfurization rate is 98.0%.
[0059] After the rich liquid is desorbed by the second-effect evaporator, SO 2 , to obtain liquid SO after condensation and compression 2 236kg / h. The desorbed solutio...
PUM
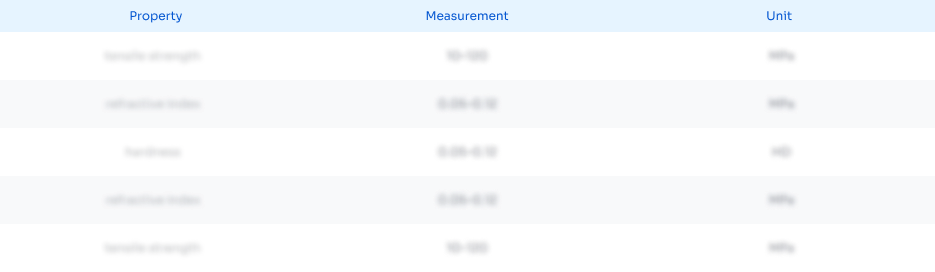
Abstract
Description
Claims
Application Information

- R&D
- Intellectual Property
- Life Sciences
- Materials
- Tech Scout
- Unparalleled Data Quality
- Higher Quality Content
- 60% Fewer Hallucinations
Browse by: Latest US Patents, China's latest patents, Technical Efficacy Thesaurus, Application Domain, Technology Topic, Popular Technical Reports.
© 2025 PatSnap. All rights reserved.Legal|Privacy policy|Modern Slavery Act Transparency Statement|Sitemap|About US| Contact US: help@patsnap.com