Method and device for cleanly storing and feeding coal slurry fuel of electric power plant
A coal slime and power plant technology, which is applied in the field of clean storage and transportation of coal slime fuel and feeding materials in power plants, can solve the problems of coal slime channel clogging, power plant boiler slime supply interruption, and feeding equipment easy to coke and block, etc.
- Summary
- Abstract
- Description
- Claims
- Application Information
AI Technical Summary
Problems solved by technology
Method used
Image
Examples
Embodiment 1
[0067] This embodiment mainly includes: coal slime rubbing equipment 1, horizontal mixing bin 2, gate valve 3, pre-pressed feeding screw 4, coal slime delivery pump 5, coal slime delivery pipeline 6, boiler slime feeder 7 , Boiler 8, coal slime rubbing equipment 1 is located above the horizontal mixing bin 2; One end is connected with the coal slime delivery pump 5, and the other end is connected with the boiler slime feeder 7, and the boiler slime feeder 7 is installed on the top of the boiler.
[0068] The functions and effects of each device of the present embodiment are as follows:
[0069] The coal slime rubbing equipment 1 is a pretreatment equipment for coal slime, which is used for the pretreatment process of coal slime, and crushes the coal slime into slurry.
[0070] The horizontal mixing bin 2 is the slurry storage equipment for coal slime, which is used for the slurry storage process, used to store the pretreated coal slime, and stirs the stored coal slime to prev...
Embodiment 2
[0087] This embodiment mainly includes: coal slime rubbing equipment 1, horizontal mixing bin 2, gate valve 3, pre-pressed feeding screw 4, coal slime delivery pump 5, coal slime delivery pipeline 6, boiler slime feeder 7 , boiler 8, check valve 9.
[0088] attached figure 2 It is the equipment workflow schematic diagram of embodiment 2, and its difference with embodiment 1 is, has increased check valve 9, and check valve 9 is installed between coal slime delivery pump 5 and coal slime delivery pipeline 6, described The check valve 9 is used to prevent the backflow of coal slime.
[0089] This embodiment includes the following steps:
[0090] Coal slime pretreatment process, coal slime slurry storage process, coal slime feeding process, coal slime pumping process, pipe flow non-return process, coal slime boiler feeding process.
[0091] After the coal slime is pumped out by the coal slime delivery pump 5, it first enters the check valve 9 and then enters the coal slime del...
Embodiment 3
[0094] This embodiment mainly includes: coal slime rubbing equipment 1, horizontal mixing bin 2, gate valve 3, pre-pressed feeding screw 4, coal slime delivery pump 5, coal slime delivery pipeline 6, boiler slime feeder 7 , Boiler 8, check valve 9, telescopic tube 10.
[0095] attached image 3 It is a schematic diagram of the equipment work flow of embodiment 3, and its difference from embodiment 2 is that an expansion tube is added, and the expansion tube is installed at one or more than one position of the coal slime delivery pipeline 6, and can also be It is installed at the connection between the coal slime delivery pipeline 6 and other equipment, and allows the coal slime to pass therethrough.
[0096] Installing the telescopic tube 10 has the following advantages:
[0097] Eliminate internal stress caused by pipe installation and environment or slime temperature changes, and facilitate disassembly and maintenance when pipe blockage and other failures occur.
[0098] ...
PUM
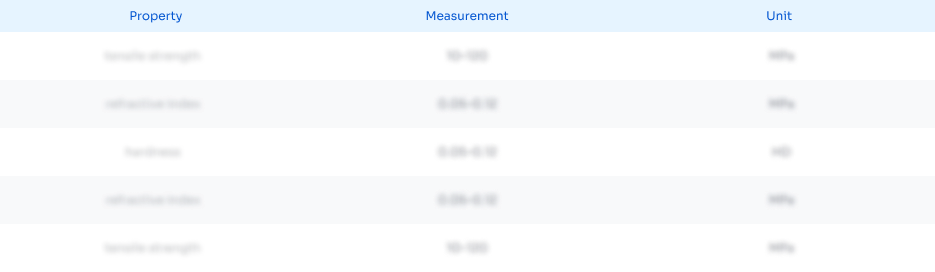
Abstract
Description
Claims
Application Information

- Generate Ideas
- Intellectual Property
- Life Sciences
- Materials
- Tech Scout
- Unparalleled Data Quality
- Higher Quality Content
- 60% Fewer Hallucinations
Browse by: Latest US Patents, China's latest patents, Technical Efficacy Thesaurus, Application Domain, Technology Topic, Popular Technical Reports.
© 2025 PatSnap. All rights reserved.Legal|Privacy policy|Modern Slavery Act Transparency Statement|Sitemap|About US| Contact US: help@patsnap.com