Ferrum-silicon-boron amorphous soft magnetic alloy modified by rare earth elements
A rare-earth element, iron-silicon-boron technology, applied in the field of amorphous soft magnetic alloy materials, can solve the problems that cannot fully meet the high saturation magnetic induction intensity, high temperature stability, limit the large-scale application of Fe-based amorphous wire, and restrict the amorphous soft magnetic alloy. The development of magnetic alloy materials and other issues, to achieve the effect of improving magnetic and mechanical properties, improving high-frequency magnetic properties, and broad market application prospects
- Summary
- Abstract
- Description
- Claims
- Application Information
AI Technical Summary
Problems solved by technology
Method used
Examples
Embodiment 1
[0019] The raw materials of each component are put into the melting furnace together, melted and smelted by conventional melting methods, and cast into amorphous iron-silicon-boron soft magnetic alloy ingots modified with rare earth elements. The contents of each component are: iron-based iron The magnetic material accounts for 76.7% of the total weight of the alloy; the vitrified element silicon accounts for 8% of the total alloy weight; the vitrified element boron accounts for 15% of the total alloy weight; and the trace rare earth element mixture accounts for 0.3% of the total alloy weight. Then take samples from the obtained alloy ingot to test its relevant properties, and compare it with the ordinary amorphous iron-silicon-boron soft magnetic alloy without adding trace rare earth element mixture. The results are shown in Table 1. It can be seen from Table 1 that the rare earth modified The properties of crystalline FeSiB soft magnetic alloy are obviously better than ordina...
Embodiment 2
[0021] The raw materials of each component are put into the melting furnace together, melted and smelted by conventional melting methods, and cast into amorphous iron-silicon-boron soft magnetic alloy ingots modified with rare earth elements. The contents of each component are: iron-based iron The magnetic material accounts for 76.9% of the total weight of the alloy; the vitrified element silicon accounts for 9% of the total alloy weight; the vitrified element boron accounts for 14% of the total alloy weight; and the trace rare earth element mixture accounts for 0.1% of the total alloy weight. Then take a sample from the obtained alloy ingot to test its relevant properties, the results are as follows: Saturation magnetic induction B s (T) is 1.6; the coercive force (A / m) is 2, the maximum magnetic permeability μ is 200,000, the iron loss (W / Kg) p50hz is 0.12, and the resistivity (mw-cm) is 130.
Embodiment 3
[0023] The raw materials of each component are put into the melting furnace together, melted and smelted by conventional melting methods, and cast into an amorphous iron-silicon-boron soft magnetic alloy ingot modified with rare earth elements. The contents of each component are: cobalt-based iron The magnetic material accounts for 76.8% of the total weight of the alloy; the vitrified element silicon accounts for 7% of the total alloy weight; the vitrified element boron accounts for 16% of the total alloy weight; and the trace rare earth element mixture accounts for 0.2% of the total alloy weight. Then take a sample from the obtained alloy ingot to test its relevant properties, the results are as follows: Saturation magnetic induction B s (T) is 0.75; coercivity (A / m) is 1.2; maximum permeability μ is 400,000; unit loss (W / Kg) P1 / 400 is 1.5.
[0024] In the above three embodiments, the ferromagnetic materials, vitrification elements and trace rare earth element mixtures used a...
PUM
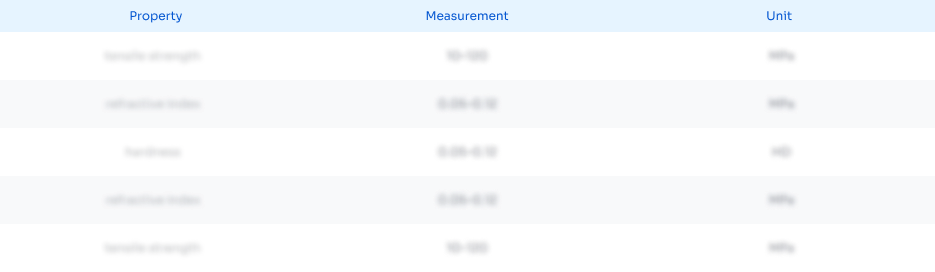
Abstract
Description
Claims
Application Information

- R&D
- Intellectual Property
- Life Sciences
- Materials
- Tech Scout
- Unparalleled Data Quality
- Higher Quality Content
- 60% Fewer Hallucinations
Browse by: Latest US Patents, China's latest patents, Technical Efficacy Thesaurus, Application Domain, Technology Topic, Popular Technical Reports.
© 2025 PatSnap. All rights reserved.Legal|Privacy policy|Modern Slavery Act Transparency Statement|Sitemap|About US| Contact US: help@patsnap.com