Self-heating floor and manufacturing method thereof
A production method and flooring technology, applied in heating methods, electric heating systems, household heating, etc., can solve problems such as potential safety hazards, and achieve the effects of preventing air bubbles, ensuring safety, and avoiding swelling
- Summary
- Abstract
- Description
- Claims
- Application Information
AI Technical Summary
Problems solved by technology
Method used
Image
Examples
Embodiment Construction
[0020] The present invention will be further described below in conjunction with the accompanying drawings.
[0021] see Figure 1-2 As shown, a self-heating floor includes a substrate 6, a surface layer 1, a conductive heating sheet 9 arranged between the substrate 6 and the surface layer 1, the conductive heating sheet 9 includes a glass fiber epoxy resin base layer 5, and is arranged on a glass The conductive heating layer 3 on the upper surface of the fiber epoxy resin base layer 5, the upper flame retardant protective layer 2 covering the upper surface of the glass fiber epoxy resin base layer 5 and covering the conductive heating layer 3, and the upper flame retardant protective layer 2 covered on the glass fiber epoxy resin layer The lower flame retardant protective layer 10 on the lower surface of the base layer 5 , the upper flame retardant protective layer 2 is bonded on the lower surface of the surface layer 1 , and the lower flame retardant protective layer 10 is b...
PUM
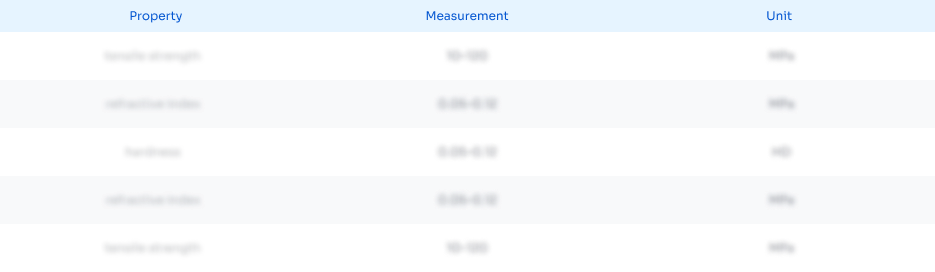
Abstract
Description
Claims
Application Information

- R&D Engineer
- R&D Manager
- IP Professional
- Industry Leading Data Capabilities
- Powerful AI technology
- Patent DNA Extraction
Browse by: Latest US Patents, China's latest patents, Technical Efficacy Thesaurus, Application Domain, Technology Topic, Popular Technical Reports.
© 2024 PatSnap. All rights reserved.Legal|Privacy policy|Modern Slavery Act Transparency Statement|Sitemap|About US| Contact US: help@patsnap.com