Spinning head
A spinneret and filament technology, which is used in spinneret assemblies, textiles, and papermaking, etc., can solve the problems of overlapping melt inlets and sealing of melt inlets.
- Summary
- Abstract
- Description
- Claims
- Application Information
AI Technical Summary
Problems solved by technology
Method used
Image
Examples
Embodiment Construction
[0024] figure 1 A first exemplary embodiment of the spinneret according to the invention is illustrated by way of example in a cross-sectional view. The exemplary embodiment comprises a nozzle holder 1 which has a nozzle receptacle 4 on its bottom side which extends between heating jackets 5 . In the central region of the nozzle receptacle 4 there is an adapter plate 2 which is fixedly connected to the nozzle holder 1 . The adapter plate 2 has two melt connections 9.1 and 9.2, which are in any case connected in the usual manner to a spinning pump (not shown here) via distribution lines .
[0025] Arranged below the adapter plate 2 is an inlet plate 3 , which is connected to the adapter plate 2 in a rotationally fixed manner via a plurality of fastening devices 8 . The inlet plate 3 has melt feed channels 6 . 1 and 6 . 2 , which are adjacent to one another and are assigned to melt connections 9 . 1 and 9 . 2 in the adapter plate 2 . The parting surfaces between the melt con...
PUM
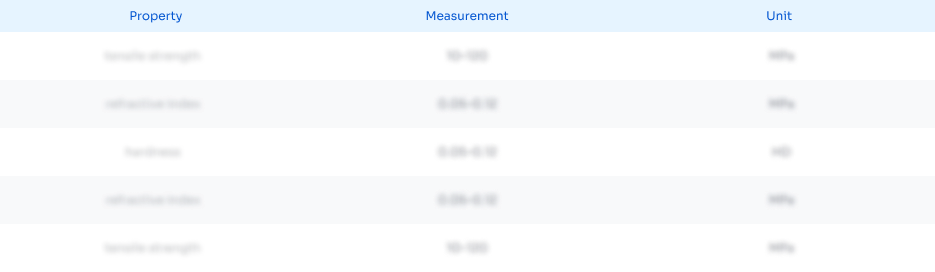
Abstract
Description
Claims
Application Information

- Generate Ideas
- Intellectual Property
- Life Sciences
- Materials
- Tech Scout
- Unparalleled Data Quality
- Higher Quality Content
- 60% Fewer Hallucinations
Browse by: Latest US Patents, China's latest patents, Technical Efficacy Thesaurus, Application Domain, Technology Topic, Popular Technical Reports.
© 2025 PatSnap. All rights reserved.Legal|Privacy policy|Modern Slavery Act Transparency Statement|Sitemap|About US| Contact US: help@patsnap.com