Method for dipping capacitor for energy-saving lamp
A technology for capacitors and energy-saving lamps, applied in the direction of drying/impregnating machines, etc., can solve the problems of insufficient impregnation of epoxy encapsulation materials, poor voltage resistance performance, and dielectric damage, etc., to ensure consistency and stability, and improve the bearing capacity Effects of current capability, reliability and life improvement
- Summary
- Abstract
- Description
- Claims
- Application Information
AI Technical Summary
Problems solved by technology
Method used
Examples
Embodiment Construction
[0011] A method for impregnating capacitors for energy-saving lamps, comprising the following steps:
[0012] (a) Put the inner sealing material in a vacuum degassing machine and stir for 10-15 minutes to defoam, and take out the impregnating material after there is no bubble;
[0013] (b) Send the capacitor core into the tunnel preheating oven for preheating, the preheating temperature is 90-110°C, and the time is 30-60 minutes;
[0014] (c) Vacuum first and then impregnate when sealing inside, the vacuum degree reaches ≥ 0.09Mpa, only one time of internal impregnation, and the impregnation time is 40-60 seconds;
[0015] (d) Heat treatment after inner sealing: first, the temperature is 90-100°C for 50-70 minutes, and then the temperature is 110-120°C for 110-130 minutes.
PUM
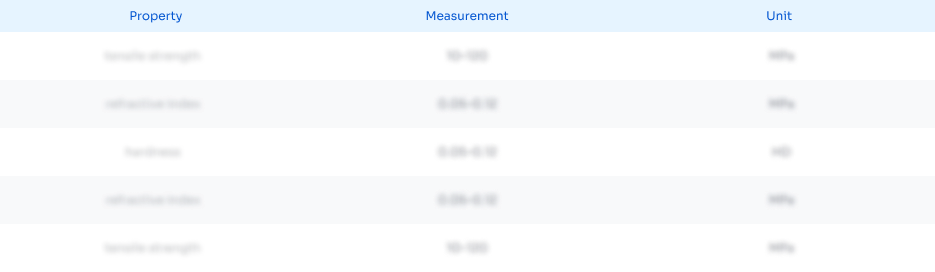
Abstract
Description
Claims
Application Information

- R&D
- Intellectual Property
- Life Sciences
- Materials
- Tech Scout
- Unparalleled Data Quality
- Higher Quality Content
- 60% Fewer Hallucinations
Browse by: Latest US Patents, China's latest patents, Technical Efficacy Thesaurus, Application Domain, Technology Topic, Popular Technical Reports.
© 2025 PatSnap. All rights reserved.Legal|Privacy policy|Modern Slavery Act Transparency Statement|Sitemap|About US| Contact US: help@patsnap.com