Vermiculizer for thin-wall cast iron and melting method thereof
A technology of vermicular agent and cast iron, which is applied in the field of cast iron vermicular agent, can solve problems such as difficulty in using and managing casting returned materials, affecting cutting performance of castings, and contamination of furnace materials, and achieves simple and stable vermicular treatment process and wide range of vermicularization Wide, easy to manage and use
- Summary
- Abstract
- Description
- Claims
- Application Information
AI Technical Summary
Problems solved by technology
Method used
Examples
Embodiment 1
[0077] Chemical composition of vermicular agent (by weight): rare earth (RE) 25.00%, silicon (Si) 38.03%, magnesium (Mg) 3.07%, calcium (Ca) 3.32%, zinc (Zn) 1.74%, magnesium oxide (MgO ) 0.66%, and the balance is iron (Fe) or unavoidable impurities 28.18%.
[0078] The vermicular agent for melting the above components uses the following raw materials and proportions: rare earth ferrosilicon (FeSiRE) 80.0%, silicon calcium alloy (FeSiCa) 12.0%, magnesium ingot (Mg) 4.5%, zinc ingot (Zn) 3.5%. According to the above ratio, the raw materials are put into the electric furnace and melted according to the following melting process.
[0079] The melting process is the same as the aforementioned process steps.
Embodiment 2
[0081] Chemical composition (by weight): rare earth (RE18.41%, silicon (Si) 45.00%, magnesium (Mg) 2.50%, calcium (Ca) 2.02%, zinc (Zn) 3.50%, magnesium oxide (MgO ) 0.60%, and the balance is iron (Fe) or unavoidable impurities 27.97%.
[0082] The vermicular agent for melting the above components adopts the following raw materials and proportions: rare earth ferrosilicon (FeSiRE) 60.0%, ferrosilicon (FeSi) 21.0%, silicon calcium alloy (FeSiCa) 7.5%, magnesium ingot (Mg) 4.2%, Zinc ingot (Zn) 7.3%. According to the above ratio, the raw materials are put into the electric furnace and melted according to the following melting process.
[0083] The melting process is the same as the aforementioned process steps.
Embodiment 3
[0085] Chemical composition (by weight): rare earth (RE) 15.00%, silicon (Si) 35.00%, magnesium (Mg) 3.17%, calcium (Ca) 4.00%, zinc (Zn) 2.13%, magnesium oxide (MgO ) 0.70%, the balance is iron (Fe) or unavoidable impurities 40%.
[0086] The vermicular agent for melting the above components adopts the following raw materials and proportions: rare earth ferrosilicon (FeSiRE) 50.0%, ferrosilicon (FeSi) 8.50%, silicon calcium alloy (FeSiCa) 15.0%, magnesium ingot (Mg) 4.5%, Zinc ingot (Zn) 6.0%, steel scrap 16.0%. According to the above ratio, the raw materials are put into the electric furnace and melted according to the following melting process.
[0087] The melting process is the same as the aforementioned process steps.
PUM
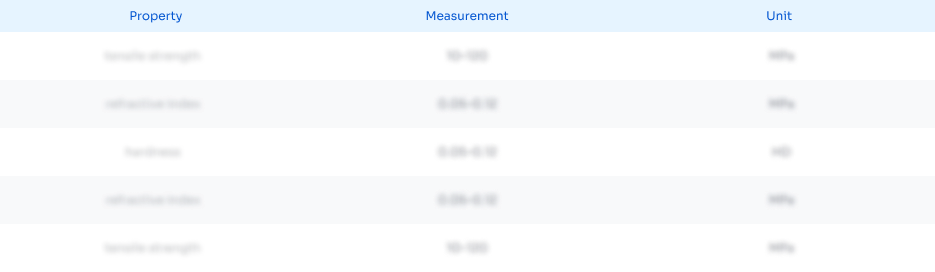
Abstract
Description
Claims
Application Information

- Generate Ideas
- Intellectual Property
- Life Sciences
- Materials
- Tech Scout
- Unparalleled Data Quality
- Higher Quality Content
- 60% Fewer Hallucinations
Browse by: Latest US Patents, China's latest patents, Technical Efficacy Thesaurus, Application Domain, Technology Topic, Popular Technical Reports.
© 2025 PatSnap. All rights reserved.Legal|Privacy policy|Modern Slavery Act Transparency Statement|Sitemap|About US| Contact US: help@patsnap.com