Method for preparing active dye detergent based on chitosan/gelatin composite material
A technology of composite materials and reactive dyes, which is applied in the field of preparation of reactive dye detergents based on chitosan/gelatin composite materials, can solve the problems of poor biodegradability, low hard water resistance, and large amount of detergents, and achieve easy Biodegradation, steam saving, good adsorption effect
- Summary
- Abstract
- Description
- Claims
- Application Information
AI Technical Summary
Problems solved by technology
Method used
Examples
Embodiment 1
[0018] 1) Preparation of aqueous phase solution: at first dissolving chitosan with a degree of deacetylation of 96% in the acetic acid solution of 2% by volume to obtain a chitosan solution with a mass percent concentration of 0.5%, then dissolving gelatin in water Obtaining a gelatin solution with a mass concentration of 3%;
[0019] By chitosan: gelatin is 1: 1 mass ratio chitosan solution and gelatin solution are mixed to obtain chitosan / gelatin solution;
[0020] 2) Emulsion preparation: add emulsifier to liquid paraffin to obtain a mixed solution of liquid paraffin and emulsifier by volume ratio of emulsifier: liquid paraffin=1:300, said emulsifier is Span 80 and Tween 80, wherein The volume ratio of Span 80 and Tween 80 is 1: 1; then chitosan / gelatin solution is added to the mixed solution of liquid paraffin and emulsifier by the volume ratio of chitosan / gelatin solution: liquid paraffin=1:4 medium, emulsified at 25°C for 25 minutes to obtain an emulsion;
[0021] 3) C...
Embodiment 2
[0024] 1) Preparation of aqueous phase solution: at first dissolving chitosan with a degree of deacetylation of 94% in acetic acid solution of 3% by volume to obtain a chitosan solution with a mass percent concentration of 1%, then dissolving gelatin in water Obtaining a gelatin solution with a mass concentration of 4%;
[0025] By chitosan: gelatin is the mass ratio of 2: 1 that chitosan solution and gelatin solution are mixed to obtain chitosan / gelatin solution;
[0026] 2) Emulsion preparation: add emulsifier to liquid paraffin to obtain a mixed solution of liquid paraffin and emulsifier by volume ratio of emulsifier: liquid paraffin=1:150, said emulsifier is Span 80 and Tween 80, wherein The volume ratio of Span 80 and Tween 80 is 2: 1; then chitosan / gelatin solution is added to the mixed solution of liquid paraffin and emulsifier by the volume ratio of chitosan / gelatin solution: liquid paraffin=1:5 , emulsified at 30°C for 15 minutes to obtain an emulsion;
[0027] 3) C...
Embodiment 3
[0030] 1) Preparation of aqueous phase solution: at first dissolving chitosan with a degree of deacetylation of 92% in acetic acid solution of 4% by volume to obtain a chitosan solution with a mass percentage concentration of 2%, then dissolving gelatin in water Obtaining a gelatin solution with a mass concentration of 6%;
[0031] By chitosan: gelatin is the mass ratio of 3: 1 that chitosan solution and gelatin solution are mixed to obtain chitosan / gelatin solution;
[0032] 2) Emulsion preparation: add emulsifier to liquid paraffin to obtain a mixed solution of liquid paraffin and emulsifier by volume ratio of emulsifier: liquid paraffin=1:200, said emulsifier is Span 80 and Tween 80, wherein The volume ratio of Span 80 and Tween 80 is 4: 1; then chitosan / gelatin solution is added to the mixed solution of liquid paraffin and emulsifier by the volume ratio of chitosan / gelatin solution: liquid paraffin=1:6 medium, emulsified at 28°C for 20 minutes to obtain an emulsion;
[0...
PUM
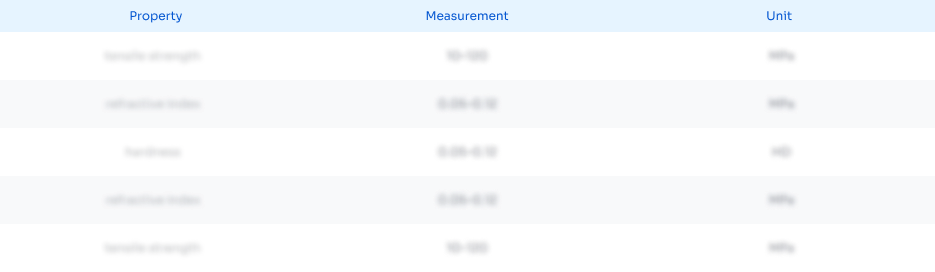
Abstract
Description
Claims
Application Information

- R&D
- Intellectual Property
- Life Sciences
- Materials
- Tech Scout
- Unparalleled Data Quality
- Higher Quality Content
- 60% Fewer Hallucinations
Browse by: Latest US Patents, China's latest patents, Technical Efficacy Thesaurus, Application Domain, Technology Topic, Popular Technical Reports.
© 2025 PatSnap. All rights reserved.Legal|Privacy policy|Modern Slavery Act Transparency Statement|Sitemap|About US| Contact US: help@patsnap.com