Micro-drill for copper alloy processing and preparation method thereof
A copper alloy and micro-drilling technology, which is applied in metal material coating process, ion implantation plating, coating, etc., can solve the problems of poor bonding between the film and the micro-drilling substrate, low film density, and low ionization rate , to achieve the effects of improved life and processing quality, low friction coefficient, and good film-base bonding force
- Summary
- Abstract
- Description
- Claims
- Application Information
AI Technical Summary
Problems solved by technology
Method used
Image
Examples
Embodiment 1
[0039] The coating machine used includes a vacuum chamber, a magnetron sputtering source, a linear ion source and a workpiece bracket with both revolution and rotation functions, and the workpiece bracket is installed inside the vacuum chamber.
[0040] (1) Ultrasonic cleaning the micro-drill substrate in trichlorethylene, after drying, wind its tip with copper wire for shielding, and then install it on the workpiece bracket, arrange the magnetron sputtering source and linear ion source, so that the magnetron A sputtering source and a linear ion source surround the microdrill substrate.
[0041] (2) A chromium target made of simple chromium is installed on the magnetron sputtering source, and the vacuum chamber is evacuated to a pressure of 1.6×10 -5 After Torr, argon gas was introduced, the linear ion source was turned on, the negative bias voltage of the micro-drill substrate was adjusted to 200V, and the surface of the micro-drill substrate was bombarded with ions for 40 mi...
Embodiment 2
[0046] The coating machine used includes a vacuum chamber, a magnetron sputtering source, a linear ion source and a workpiece bracket with both revolution and rotation functions, and the workpiece bracket is installed inside the vacuum chamber.
[0047] (1) Ultrasonic cleaning the micro-drill substrate in absolute ethanol, after drying, wrap its tip with iron wire to shield, and then install it on the workpiece bracket, arrange the magnetron sputtering source and linear ion source, so that the magnetron sputtering The radiation source and the linear ion source surround the microdrill substrate.
[0048] (2) Install a titanium target made of elemental titanium on the magnetron sputtering source, and evacuate the vacuum chamber to a pressure of 2.0×10 -5 After Torr, argon gas was introduced, the linear ion source was turned on, the negative bias voltage of the micro-drill substrate was adjusted to 100V, ion bombardment was performed on the surface of the micro-drill substrate, a...
PUM
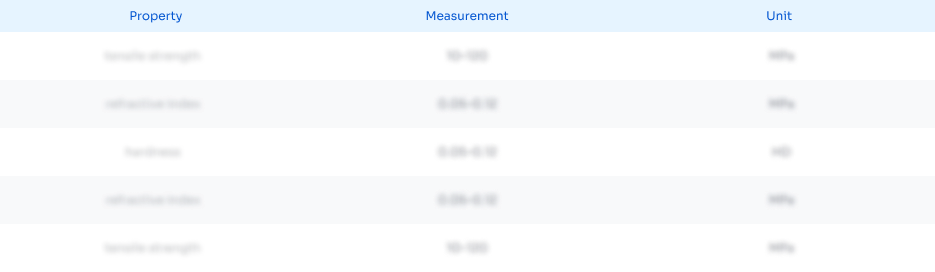
Abstract
Description
Claims
Application Information

- R&D
- Intellectual Property
- Life Sciences
- Materials
- Tech Scout
- Unparalleled Data Quality
- Higher Quality Content
- 60% Fewer Hallucinations
Browse by: Latest US Patents, China's latest patents, Technical Efficacy Thesaurus, Application Domain, Technology Topic, Popular Technical Reports.
© 2025 PatSnap. All rights reserved.Legal|Privacy policy|Modern Slavery Act Transparency Statement|Sitemap|About US| Contact US: help@patsnap.com