Supported SCR denitration catalyst of medium and low temperature flue gas and preparation method and application thereof
A denitration catalyst, low temperature flue gas technology, applied in catalyst activation/preparation, chemical instruments and methods, physical/chemical process catalysts, etc. Strong sulfur poisoning ability, strong anti-sulfur poisoning, simple preparation effect
- Summary
- Abstract
- Description
- Claims
- Application Information
AI Technical Summary
Problems solved by technology
Method used
Image
Examples
Embodiment 1
[0028] (1) Catalyst preparation
[0029] First, 4g oxalic acid (C 2 h 2 o 4 ·H 2 O) Dissolve in 20mL 60°C deionized water; add 0.51g ammonium metavanadate (in V 2 o 5 Accounting for 2wt% of the total catalyst content) and 2.43g copper nitrate trihydrate (Cu(NO 3 ) 2 ·3H 2 O) and 2.26g manganese acetate tetrahydrate (Mn(CH 3 COO) 2 4H 2 O) (with CuO and MnO 2 Accounting for 8wt% of the total catalyst content), fully stirred to obtain mixed metal salt solution; 18g anatase TiO 2 Add it into the mixed metal salt solution (accounting for 90wt% of the total catalyst content), stir for 4 hours, and dry at 90°C for 24 hours. mesh particles to obtain a loaded SCR denitrification catalyst for medium and low temperature flue gas, which is ready for use.
[0030] (2) Catalyst evaluation
[0031] Put the catalyst obtained above into a stainless steel reaction tube, and use a programmed temperature controller to heat the fixed-bed reactor to a certain temperature (200-350°C);...
Embodiment 2
[0035] (1) Catalyst preparation
[0036] First add about 3g of oxalic acid (C 2 h 2 o 4 ·H 2 O) dissolved in 20mL 50°C deionized water; add 0.26g ammonium metavanadate (in V 2 o 5 Accounting for 2wt% of the total catalyst content) and 6.77g manganese acetate tetrahydrate (Mn(CH 3 COO) 2 4H 2 O) (as MnO 2 Accounting for 12wt% of the total catalyst content), fully stirred to obtain mixed metal salt solution; 17.2g gamma-Al 2 o 3 Add it into the mixed metal salt solution (accounting for 86wt% of the total catalyst content), stir for 2 hours, and then dry it at 140°C for 8 hours. mesh particles to obtain a loaded SCR denitrification catalyst for medium and low temperature flue gas, which is ready for use.
[0037] (2) Catalyst evaluation
[0038] The catalyst evaluation process is as in Example 1.
[0039] Catalyst evaluation results such as figure 1 Shown, in volume concentration [NO]=[NH 3 ]=0.1%, [O 2 ]=3%, air speed=6.6,000h -1 Under operating conditions, NO a...
Embodiment 3
[0041] (1) Catalyst preparation
[0042] First about 7g of oxalic acid (C 2 h 2 o 4 ·H 2 O) Dissolve in 25mL 80°C deionized water; add 0.65g ammonium metavanadate (in V 2 o 5 Accounting for 2.5wt% of the total catalyst content) and 3.04g iron nitrate nonahydrate (Fe(NO 3 ) 3 9H 2 O), 1.69g manganese acetate tetrahydrate (Mn(CH 3 COO) 2 4H 2 O) and 2.18g cobalt nitrate hexahydrate (Co(NO 3 ) 2 ·6H 2 O) (as Fe 2 o 3 , MnO 2 and Co 3 o 4 Accounting for 9wt% of the total catalyst content), fully stirred to obtain mixed metal salt solution; 12g anatase TiO 2 and 5.7g γ-Al 2 o 3 Add it into the mixed metal salt solution (accounting for 88.5wt% of the total catalyst content), stir for 6 hours, and then dry it at 160°C for 12 hours. 80 mesh particles to obtain a loaded SCR denitrification catalyst for medium and low temperature flue gas, which is ready for use.
[0043] (2) Catalyst evaluation
[0044] The catalyst evaluation process is as in Example 1.
[0045...
PUM
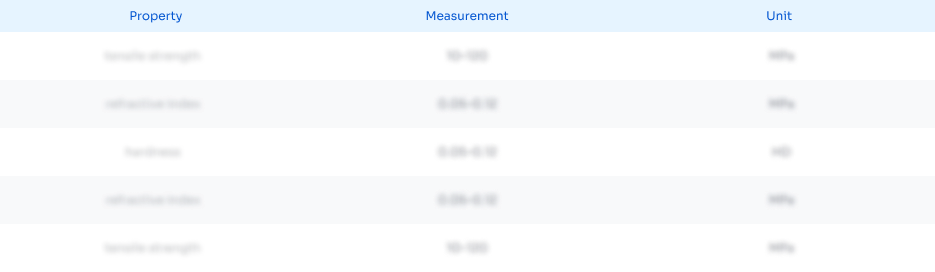
Abstract
Description
Claims
Application Information

- R&D Engineer
- R&D Manager
- IP Professional
- Industry Leading Data Capabilities
- Powerful AI technology
- Patent DNA Extraction
Browse by: Latest US Patents, China's latest patents, Technical Efficacy Thesaurus, Application Domain, Technology Topic, Popular Technical Reports.
© 2024 PatSnap. All rights reserved.Legal|Privacy policy|Modern Slavery Act Transparency Statement|Sitemap|About US| Contact US: help@patsnap.com