Dyeing process using reducing and bleeding
A process and wash-out technology, applied in the field of wash-out dyeing process, which can solve the problems of not being resistant to chlorine bleaching, poor rubbing fastness, affecting LOT color after washing, etc.
- Summary
- Abstract
- Description
- Claims
- Application Information
AI Technical Summary
Problems solved by technology
Method used
Examples
Embodiment 1
[0011] The process of the reduction, washing and fading dyeing process of the present invention is as follows: semi-finished white cloth → padding dyeing solution process → first drying process → padding reducing solution process → steaming process → water washing process → oxidation process → soaping process → Washing process → second drying process → padding softening process → tentering process → pre-shrinking process → finished product.
[0012] Among them, steaming process, water washing process, oxidation process, soaping process, water washing process, second drying process, padding and softening process, tentering process and pre-shrinking process are conventional processing processes in this industry.
[0013] in:
[0014] Padding dyeing process: according to the color of the fabric to be dyed, add a corresponding amount of dye in the water bath, pad at room temperature, and the speed is 30 m / min. The dye used is a mixture of vat dyes and sulfur dyes in a weight rati...
Embodiment 2
[0018] The process of the reduction, washing and fading dyeing process of the present invention is as follows: semi-finished white cloth → padding dyeing solution process → first drying process → padding reducing solution process → steaming process → water washing process → oxidation process → soaping process → Washing process → second drying process → padding softening process → tentering process → pre-shrinking process → finished product.
[0019] Among them, steaming process, water washing process, oxidation process, soaping process, water washing process, second drying process, padding and softening process, tentering process and pre-shrinking process are conventional processing processes in this industry.
[0020] in:
[0021] Padding dyeing process: according to the color of the fabric to be dyed, add a corresponding amount of dye in the water bath, pad at room temperature, and the speed is 45 m / min. The dye used is a mixture of vat dyes and sulfur dyes in a weight rati...
Embodiment 3
[0025] The process of the reduction, washing and fading dyeing process of the present invention is as follows: semi-finished white cloth → padding dyeing solution process → first drying process → padding reducing solution process → steaming process → water washing process → oxidation process → soaping process → Washing process → second drying process → padding softening process → tentering process → pre-shrinking process → finished product.
[0026] Among them, steaming process, water washing process, oxidation process, soaping process, water washing process, second drying process, padding and softening process, tentering process and pre-shrinking process are conventional processing processes in this industry.
[0027] in:
[0028] Padding dyeing process: according to the color of the fabric to be dyed, add a corresponding amount of dye in the water bath, pad at room temperature, and the speed is 60 m / min. The dye used is a mixture of vat dyes and sulfur dyes in a weight rati...
PUM
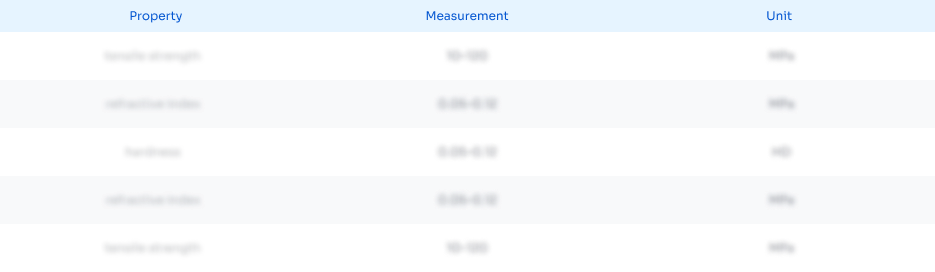
Abstract
Description
Claims
Application Information

- R&D
- Intellectual Property
- Life Sciences
- Materials
- Tech Scout
- Unparalleled Data Quality
- Higher Quality Content
- 60% Fewer Hallucinations
Browse by: Latest US Patents, China's latest patents, Technical Efficacy Thesaurus, Application Domain, Technology Topic, Popular Technical Reports.
© 2025 PatSnap. All rights reserved.Legal|Privacy policy|Modern Slavery Act Transparency Statement|Sitemap|About US| Contact US: help@patsnap.com