Method for preparing porous mullite
A porous mullite, mass percentage technology, applied in ceramic products, applications, household appliances, etc., can solve the problems of poor high temperature resistance, difficult synthesis process, control danger, etc., to improve strength, improve high temperature resistance, The effect of reducing the residual glass phase
- Summary
- Abstract
- Description
- Claims
- Application Information
AI Technical Summary
Problems solved by technology
Method used
Image
Examples
Embodiment 1
[0022] 5g of fly ash, 3g of bauxite and 2g of aluminum fluoride are mixed, ball milled and dried to a median particle size of ≤10μm. Add 5% by mass of polyethylene glycol aqueous solution and 30% by mass of starch aqueous solution to the mixed powder to make a mixed slurry with a solid content of 60% by mass; after ball milling, the slurry is injected with a size of It is molded in a 15mm×25mm×140mm mold and cured at 80°C in a constant temperature drying oven. After demoulding, the dried green body is kept at 400°C for 0.5h, and then at 1500°C for 2h.
Embodiment 2
[0024] 5g of fly ash, 3.5g of bauxite and 1.5g of aluminum fluoride are mixed, and ball milled and dried to a median particle size of ≤10 μm. Add 10% by mass of polyethylene glycol aqueous solution and 40% by mass of starch aqueous solution to the mixed powder to make a mixed slurry with a solid content of 65% by mass; after ball milling, the slurry is injected with a size of Molded in a 15mm×25mm×140mm mold and cured at 70°C in a constant temperature drying oven, the dried green body after demoulding was kept at 350°C for 1.5h, and then at 1400°C for 3h.
Embodiment 3
[0026] 5g of fly ash, 4g of bauxite and 1g of aluminum fluoride are mixed, and ball milled and dried until the median particle size is less than or equal to 10 μm. Add 8% by mass of polyethylene glycol aqueous solution and 35% by mass of starch aqueous solution to the mixed powder to make a mixed slurry with a solid phase content of 70% by mass; after ball milling, the slurry is injected with a size of It is molded in a 15mm×25mm×140mm mold and cured at 75°C in a constant temperature drying oven. After demoulding, the dried body is kept at 350°C for 2 hours, and then at 1300°C for 4 hours.
PUM
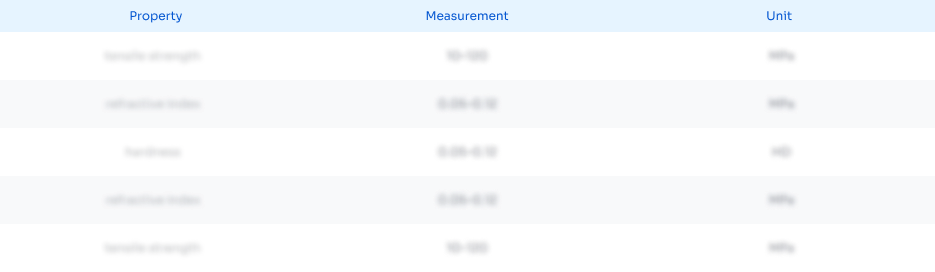
Abstract
Description
Claims
Application Information

- R&D
- Intellectual Property
- Life Sciences
- Materials
- Tech Scout
- Unparalleled Data Quality
- Higher Quality Content
- 60% Fewer Hallucinations
Browse by: Latest US Patents, China's latest patents, Technical Efficacy Thesaurus, Application Domain, Technology Topic, Popular Technical Reports.
© 2025 PatSnap. All rights reserved.Legal|Privacy policy|Modern Slavery Act Transparency Statement|Sitemap|About US| Contact US: help@patsnap.com