Method for rolling grinding of ground surface of single crystal silicon
A monocrystalline silicon grinding technology, which is applied in grinding/polishing equipment, machine tools suitable for grinding workpiece planes, machine tools suitable for grinding workpiece edges, etc., can solve the problems of time-consuming and labor-consuming, difficult to control rotation, Heavy weight and other problems, to achieve the effect of simplifying the grinding process, improving quality and improving work efficiency
- Summary
- Abstract
- Description
- Claims
- Application Information
AI Technical Summary
Problems solved by technology
Method used
Image
Examples
Embodiment Construction
[0037] The following describes the implementation of the present invention through specific specific examples, and those skilled in the art can easily understand other advantages and effects of the present invention from the content disclosed in this specification. The present invention can also be implemented or applied in other different specific embodiments, and various details in this specification can also be modified or changed based on different viewpoints and applications without departing from the spirit of the present invention.
[0038] See Figure 2a To Figure 2i and Figure 3a to Figure 3b , Which is shown as a schematic diagram of the embodiment of the method for grinding surface spheronization of single crystal silicon of the present invention. It should be noted that the drawings are simplified schematic diagrams, and the basic idea of the present invention is only schematically illustrated, so The drawing only shows the components related to the invented single ...
PUM
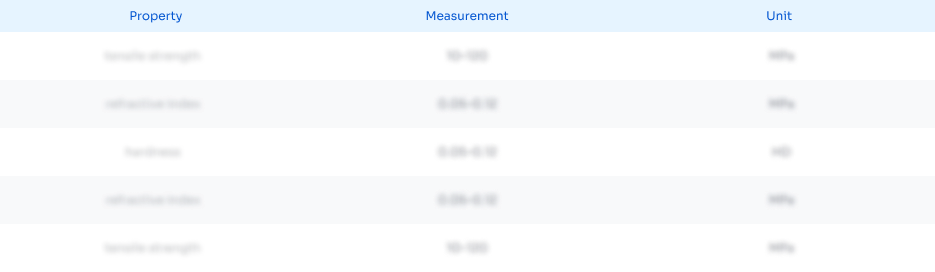
Abstract
Description
Claims
Application Information

- R&D Engineer
- R&D Manager
- IP Professional
- Industry Leading Data Capabilities
- Powerful AI technology
- Patent DNA Extraction
Browse by: Latest US Patents, China's latest patents, Technical Efficacy Thesaurus, Application Domain, Technology Topic, Popular Technical Reports.
© 2024 PatSnap. All rights reserved.Legal|Privacy policy|Modern Slavery Act Transparency Statement|Sitemap|About US| Contact US: help@patsnap.com