Preparation method for metal ceramic composite special-shaped piece
A technology of metal-ceramic composite and special-shaped parts, which is applied in the field of preparation of metal-ceramic composite special-shaped parts, which can solve the problems of difficult-to-form metal-ceramic composite special-shaped parts, difficulty in connecting ceramics and metals, etc., and achieve the effect of forming and avoiding deformation
- Summary
- Abstract
- Description
- Claims
- Application Information
AI Technical Summary
Problems solved by technology
Method used
Examples
specific Embodiment approach 1
[0012] Specific Embodiment 1: The steps of the preparation method of the metal-ceramic composite special-shaped parts in this embodiment are: Step 1: Select ceramic powder and metal powder, and the difference between the sintering temperature of the ceramic powder and the sintering temperature of the metal powder is between 0-100°C between;
[0013] Step 2: Select an organic binder;
[0014] Step 3: Preparation of feed material, put the ceramic powder with a loading capacity of 48-60% into the mixer and heat it to 100-300°C, then add an organic binder for mixing and granulation, and the kneading and granulation The time is 1-2 hours, and the cylindrical ceramic feed material with a length of 3-5mm and a diameter of 2mm is made, and the metal powder with a loading capacity of 48-60% is put into a mixer and heated to 100-300°C, and then Then add an organic binder for mixing and granulation. The mixing and granulation time is 1-2 hours to make a cylindrical metal feed with a len...
specific Embodiment approach 2
[0019] Embodiment 2: This embodiment differs from Embodiment 1 in that the ceramic powder in step 1 is composed of one or more of zinc oxide, zirconium oxide, aluminum oxide, silicon nitride, and silicon carbide. When two or more of the above components are mixed, an appropriate mixing ratio can be selected according to the wear resistance, corrosion resistance and high temperature usability of the desired product, so as to obtain a metal-ceramic composite special-shaped part that meets actual needs.
specific Embodiment approach 3
[0020] Embodiment 3: The difference between this embodiment and Embodiment 1 or 2 is that the metal powder in step 1 is composed of one or more of nickel-based superalloys, molybdenum alloys, niobium-silicon alloys, and cobalt-based superalloys. . When two or more of the above components are mixed, an appropriate mixing ratio can be selected according to the wear resistance, corrosion resistance and high temperature usability of the desired product, so as to obtain a metal-ceramic composite special-shaped part that meets actual needs.
PUM
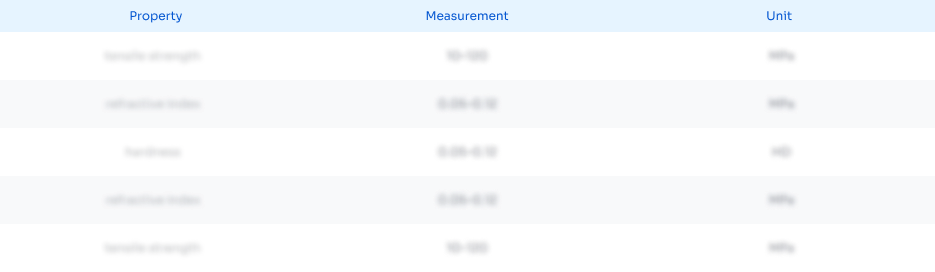
Abstract
Description
Claims
Application Information

- R&D Engineer
- R&D Manager
- IP Professional
- Industry Leading Data Capabilities
- Powerful AI technology
- Patent DNA Extraction
Browse by: Latest US Patents, China's latest patents, Technical Efficacy Thesaurus, Application Domain, Technology Topic, Popular Technical Reports.
© 2024 PatSnap. All rights reserved.Legal|Privacy policy|Modern Slavery Act Transparency Statement|Sitemap|About US| Contact US: help@patsnap.com