Catalyst for removing traces of oxygen in catalytic cracking dry gas
A catalytic cracking and catalyst technology, applied in physical/chemical process catalysts, metal/metal oxide/metal hydroxide catalysts, chemical change purification/separation, etc. Can not use FCC dry gas deoxidation process and other problems to achieve the effect of easy operation, not easy to fly over temperature, and strong anti-poisoning ability
- Summary
- Abstract
- Description
- Claims
- Application Information
AI Technical Summary
Problems solved by technology
Method used
Examples
Embodiment 1
[0025] made by the rolling ball method θ-Al 2 o 3 200 g of balls were impregnated with 300 ml of 5% KOH solution for 20 minutes, then dried in a drying oven at 200° C. for 4 hours, and set aside. 1.62g AgNO 3 Prepare 300ml aqueous solution, take spare θ-Al 2 o 3 The ball was immersed in this solution for 20 minutes, then poured off the excess liquid, placed in a drying oven at 180°C, dried for 8 hours and then cooled to room temperature. Take 0.382g PdCl 2 Make a solution with HCl, then adjust the pH value of the solution to 2.5, adjust the volume to 284ml, and then pour it onto the carrier after the first impregnation, then dry it at 80°C for 12 hours, and then bake it at 450°C for 4 hours. at 150°C with H 2 Reduction for 2 hours, cooled to room temperature, the Pd content is 0.11%, the Ag content is 0.506% active components on the catalyst eggshell-shaped distribution of deoxidation catalyst, wherein the promoter K + The content in the carrier is 1.04%.
[0026] Pa...
Embodiment 2
[0028] made by the rolling ball method θ-Al 2 o 3 100 g of balls were soaked with 150 ml of 5% KOH solution for 10 minutes, then dried in a drying oven at 180° C. for 4 hours, and set aside. 2.1g Cr(NO 3 ) 3 .9H 2O is prepared into 150ml aqueous solution, and the θ-Al 2 o 3 The balls were immersed in this solution for 30 minutes, then poured off the excess liquid, placed in a drying oven at 100°C, dried for 8 hours and then cooled to room temperature. Take 0.2gPdCl 2 Make a solution, adjust the pH value of the solution to 2.5, adjust the volume to 142ml, then pour it onto the carrier after the first impregnation, and then dry it at 100°C for 12 hours, bake it at 450°C for 4 hours, and then bake it at 150°C H 2 Reduction for 2 hours, cooled to room temperature, the Pd content is 0.109%, and the Cr content is 0.26%. The active component is an eggshell-shaped distribution of deoxidation catalyst on the catalyst, wherein the auxiliary agent K + The content in the carrie...
Embodiment 3
[0031] made by the rolling ball method θ-Al 2 o 3 40 g of balls were impregnated with 60 ml of 5% NaOH solution for 10 minutes, then dried in a drying oven at 180° C. for 4 hours, and set aside. 0.72g Co(NO 3 ) 2 .6H 2 O is prepared into 60ml aqueous solution, and the θ-Al 2 o 3 The balls were immersed in this solution for 30 minutes, then poured off the excess liquid, placed in a drying oven at 120°C, dried for 12 hours and then cooled to room temperature. Take 0.13gPdCl 2 Make a solution, adjust the pH value of the solution to 1.5, adjust the volume to 56ml, and then pour it onto the carrier after the first impregnation, and then dry it at 180°C for 12 hours, bake it at 450°C for 6 hours, and then bake it at 150°C H 2 Reduction for 4 hours, cooled to room temperature, the Pd content is 0.18%, the Co content is 0.35%, the active component is the deoxygenation catalyst with eggshell distribution on the catalyst, wherein the promoter Na + The content in the carrier i...
PUM
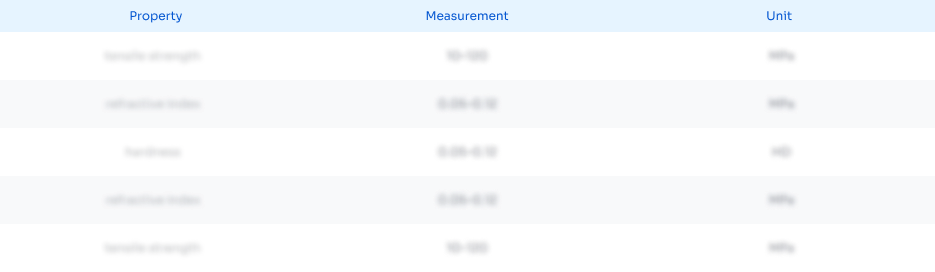
Abstract
Description
Claims
Application Information

- R&D
- Intellectual Property
- Life Sciences
- Materials
- Tech Scout
- Unparalleled Data Quality
- Higher Quality Content
- 60% Fewer Hallucinations
Browse by: Latest US Patents, China's latest patents, Technical Efficacy Thesaurus, Application Domain, Technology Topic, Popular Technical Reports.
© 2025 PatSnap. All rights reserved.Legal|Privacy policy|Modern Slavery Act Transparency Statement|Sitemap|About US| Contact US: help@patsnap.com