Combined thermochemical pretreatment and refining of lignocellulosic biomass
A lignocellulose, pretreatment technology, applied in the direction of biofuel, animal feed, animal feed, etc., can solve the problem of expensive
- Summary
- Abstract
- Description
- Claims
- Application Information
AI Technical Summary
Problems solved by technology
Method used
Image
Examples
Embodiment
[0053] Enzymatic hydrolysis was performed using an excess of enzyme to determine the theoretical maximum yield of monosaccharides using lignocellulosic material that had been pretreated using steam hydrolysis and passed through a refiner. The percentages of the sum of released glucose and xylose are shown in Table 1.
[0054] Hardwood chips underwent steam hydrolysis for 5 to 10 minutes at 160 psig in Andritz's 2 odtpd mechanical pulping system. At the outlet of the system, the pretreated lignocellulosic material is reduced in size at an elevated temperature of about 188°C and a pressure of 160 psig. The refined lignocellulosic material is then released and depressurized to a separate collector. The material is then subjected to enzymatic hydrolysis using cellulase and xylanase. The maximum theoretical sugar yield tested (Method 1) was compared with the various pretreatment methods listed in Table 1.
[0055] Table 1
[0056] Comparison of maximum theoretical sugar yield a...
PUM
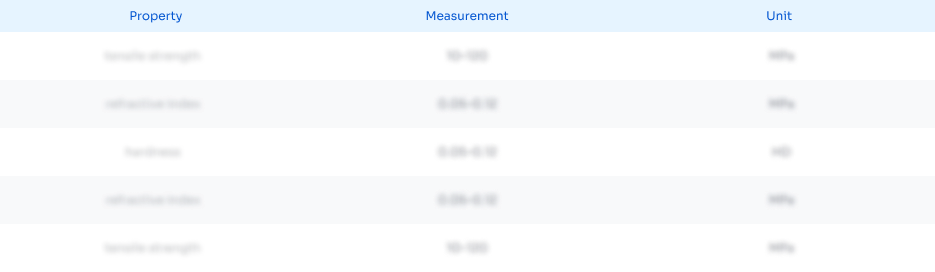
Abstract
Description
Claims
Application Information

- R&D
- Intellectual Property
- Life Sciences
- Materials
- Tech Scout
- Unparalleled Data Quality
- Higher Quality Content
- 60% Fewer Hallucinations
Browse by: Latest US Patents, China's latest patents, Technical Efficacy Thesaurus, Application Domain, Technology Topic, Popular Technical Reports.
© 2025 PatSnap. All rights reserved.Legal|Privacy policy|Modern Slavery Act Transparency Statement|Sitemap|About US| Contact US: help@patsnap.com