Motor
A technology of armature and winding, applied in the direction of electric steering mechanism, electrical components, electromechanical devices, etc., can solve the problems of increased manufacturing cost, deterioration of winding space factor, and deterioration of productivity, and achieve the effect of increasing torque
- Summary
- Abstract
- Description
- Claims
- Application Information
AI Technical Summary
Problems solved by technology
Method used
Image
Examples
Embodiment Construction
[0026] [16] Hereinafter, a first embodiment of the present invention will be described with reference to the drawings. First, based on Figure 1A The configuration of the electric power steering apparatus 20 using the motor 40 according to the first embodiment will be described. Figure 1A is a configuration diagram showing an example of the overall configuration of the electric power steering device according to the first embodiment of the present invention, Figure 1B It is a circuit block diagram showing a configuration example of the ECU 30 and the like.
[0027] [17] The electric power steering device 20 is mainly composed of a steering wheel 21, a steering shaft 22, a pinion input shaft 23, a steering wheel angle sensor 24, a reducer 27, a rack and pinion mechanism 28, a pull rod 29, an ECU 30, and a motor rotation angle The sensor 33, the motor 40, etc. constitute.
[0028] [18] If Figure 1A As shown, one end of the steering shaft 22 is connected to the steering wh...
PUM
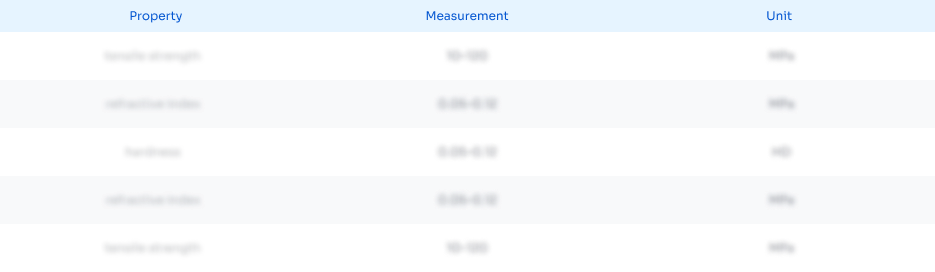
Abstract
Description
Claims
Application Information

- R&D Engineer
- R&D Manager
- IP Professional
- Industry Leading Data Capabilities
- Powerful AI technology
- Patent DNA Extraction
Browse by: Latest US Patents, China's latest patents, Technical Efficacy Thesaurus, Application Domain, Technology Topic, Popular Technical Reports.
© 2024 PatSnap. All rights reserved.Legal|Privacy policy|Modern Slavery Act Transparency Statement|Sitemap|About US| Contact US: help@patsnap.com