Water gap lining layer material for continuous casting
A lining layer and nozzle technology, which is applied in foundry equipment, casting melt containers, manufacturing tools, etc., can solve the problems of corrosion resistance, poor resistance to molten steel scouring, strict working atmosphere requirements, and short resistance to molten steel scouring. The effect of improving thermal shock performance, improving continuous casting production efficiency and long service life
- Summary
- Abstract
- Description
- Claims
- Application Information
AI Technical Summary
Problems solved by technology
Method used
Examples
Embodiment 1
[0018] As shown in Table 1: Mix 20 parts of corundum, 30 parts of fused zirconia mullite, 40 parts of ceramic hollow balls, 1 part of light-fired alumina, and 2 parts of sintering aids using a high-speed granulator, and add 2 parts Phosphate binder and 5 parts of thermosetting phenolic resin binder are mixed and granulated at high speed, and then dried in a fluidized drying bed or a rotary drying kiln. The inner lining layer is preformed with a pressure of 30-80Mpa. After the preformed inner hole body is simply trimmed, the mold is loaded, and then the body material of the continuous casting nozzle and other special required materials (such as slag strand material) are added, and then in 100 -160Mpa pressure for isostatic composite molding. Next, according to different continuous casting nozzle products, the molded products are dried, fired, machined, glazed, iron sleeves and thermal insulation fibers are installed through different process routes, and then quality inspection ...
Embodiment 2
[0019] Embodiment 2), embodiment 3), embodiment 4) and embodiment 5) refer to Table 1, which are similar to the foregoing embodiments and will not be described in detail here.
[0020] Table 1
[0021]
[0022]
PUM
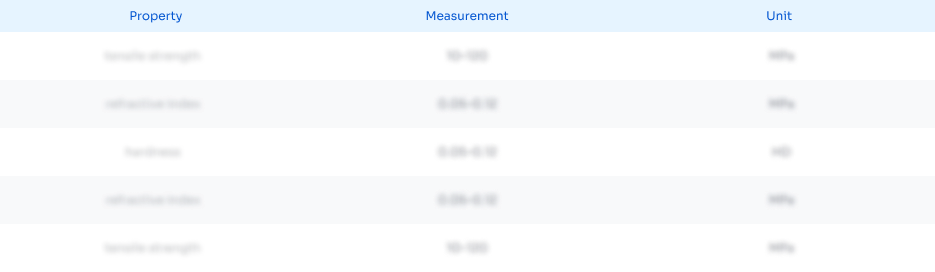
Abstract
Description
Claims
Application Information

- R&D
- Intellectual Property
- Life Sciences
- Materials
- Tech Scout
- Unparalleled Data Quality
- Higher Quality Content
- 60% Fewer Hallucinations
Browse by: Latest US Patents, China's latest patents, Technical Efficacy Thesaurus, Application Domain, Technology Topic, Popular Technical Reports.
© 2025 PatSnap. All rights reserved.Legal|Privacy policy|Modern Slavery Act Transparency Statement|Sitemap|About US| Contact US: help@patsnap.com