Warp-knitting polyester fabric and processing method thereof
A warp-knitted polyester and processing method technology, which is applied in the field of warp-knitted polyester fabrics and warp-knitted polyester fabrics, can solve the problems of suede lodging, poor gloss, unsatisfactory elasticity, etc. Guaranteed elongation and strong upright feeling
- Summary
- Abstract
- Description
- Claims
- Application Information
AI Technical Summary
Problems solved by technology
Method used
Examples
Embodiment 1
[0026] The processing door width is 140cm, the hair height is 1mm and the weight is 230g / m 2 Take the warp knitted polyester fabric as an example.
[0027] A) Raw material selection: the surface texture is selected from 50D / 36F FDY glossy yarn with a triangular cross-sectional shape, the inner layer texture is selected from 75D / 36F FDY glossy filament, and the bottom layer is selected from 40D spandex yarn. The mass percentage that accounts for in fabric is 56%, and the mass percentage that inner tissue accounts for in fabric is 37%, and the mass percentage that bottom tissue accounts for in fabric is 7%;
[0028] B) Warping: put the surface texture material selected in step A), that is, 50D / 36F FDY glossy yarn, 75D / 36F FDY glossy yarn and 40D spandex yarn into the warping machine. Warp, specifically: for 50D / 36F FDY bright yarn and 75D / 36F FDY bright yarn, the speed of the yarn is controlled at 600m / min during warping, while for 40D spandex yarn, the speed of the yarn is con...
Embodiment 2
[0036] The processing width is 150cm, the hair height is 1mm and the weight is 250g / m 2 Take the warp knitted polyester fabric as an example.
[0037] A) Raw material selection: the surface texture is selected from 50D / 36F FDY glossy yarn with a triangular cross-sectional shape, the inner layer texture is selected from 50D / 36F FDY glossy silk, and the bottom layer is selected from 40D spandex yarn. The mass percentage that accounts for in fabric is 65%, and the mass percentage that inner tissue accounts for in fabric is 27%, and the mass percentage that bottom tissue accounts for in fabric is 8%;
[0038] B) warping: put the FDY glossy silk of 50D / 36F and the spandex yarn of 40D into the warping machine for the raw materials of surface layer texture and inner layer texture selected by step A), specifically: for 50D / 36F For 36F FDY bright yarn, the speed of control yarn during warping is 600m / min, while for 40D spandex yarn, the speed of control yarn during warping is 250m / min...
Embodiment 3
[0046] The processing door width is 160cm, the hair height is 1mm and the weight is 260g / m 2 Take the warp knitted polyester fabric as an example.
[0047] A) Raw material selection: the surface texture is selected from 50D / 36F FDY glossy yarn with a triangular cross-sectional shape, the inner layer texture is selected from 50D / 36F FDY glossy silk, and the bottom layer is selected from 40D spandex yarn. The mass percentage that accounts for in fabric is 69%, and the mass percentage that inner tissue accounts for in fabric is 23.5%, and the mass percentage that bottom tissue accounts for in fabric is 7.5%;
[0048] B) warping: put the FDY glossy silk of 50D / 36F and the spandex yarn of 40D into the warping machine for the raw materials of surface layer texture and inner layer texture selected by step A), specifically: for 50D / 36F For 36F FDY bright yarn, the speed of control yarn during warping is 600m / min, while for 40D spandex yarn, the speed of control yarn during warping is...
PUM
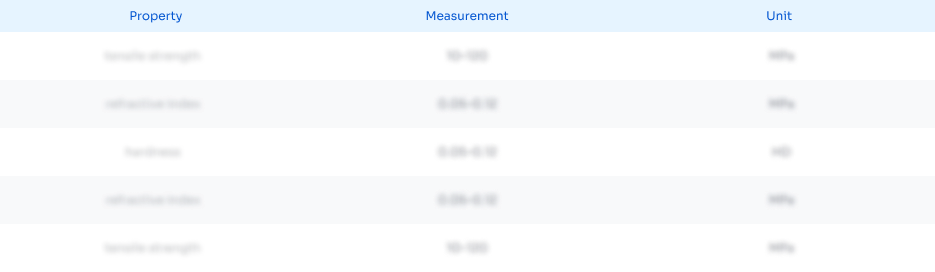
Abstract
Description
Claims
Application Information

- R&D
- Intellectual Property
- Life Sciences
- Materials
- Tech Scout
- Unparalleled Data Quality
- Higher Quality Content
- 60% Fewer Hallucinations
Browse by: Latest US Patents, China's latest patents, Technical Efficacy Thesaurus, Application Domain, Technology Topic, Popular Technical Reports.
© 2025 PatSnap. All rights reserved.Legal|Privacy policy|Modern Slavery Act Transparency Statement|Sitemap|About US| Contact US: help@patsnap.com