Hot charging thick-wall combination roller with bimetal roll cover
A bimetal, roll sleeve technology, used in metal rolling, metal rolling, rolls and other directions, can solve the problems of high energy consumption, difficult separation and recovery of precious alloys, easy to break, etc. Significant cost reduction and efficiency increase
- Summary
- Abstract
- Description
- Claims
- Application Information
AI Technical Summary
Problems solved by technology
Method used
Image
Examples
Embodiment 1
[0029] Embodiment 1: Combined rolls of the bar finishing mill
[0030] The outer layer of the roller sleeve 3 is made of high-boron high-speed steel, the inner layer is a seamless steel pipe, the mandrel 4 is made of 40Cr, the end sleeve 1 and the pressure ring 2 are made of 42CrMo, and the interference fit between the thick-walled roller sleeve 3 and the mandrel 4 Take tolerance H7 / P6, take tolerance H7 / v6 for interference fit between end sleeve 1 and mandrel 4, take tolerance H7 / v6 for interference fit between pressure ring 2, end sleeve 1 and thick-walled roller sleeve 3.
[0031] The hot-packed thick-walled roll sleeve combination roll is safe and reliable during use, and its service life is three times longer than that of the original integral roll.
Embodiment 2
[0032] Embodiment 2: angle steel combination roll
[0033] Such as image 3 As shown, the outer layer of the thick-walled roller sleeve 3 is made of high-boron high-speed steel, the mandrel 4 is made of 40Cr, the end sleeve 1 and the pressure ring 2 are made of 42CrMo, and the interference fit between the thick-walled roller sleeve 3 and the mandrel 4 is based on the tolerance H7 / P6, the interference fit between the end sleeve 1 and the mandrel 4 takes the tolerance H7 / v6, and the interference fit between the pressure ring 2 and the end sleeve 1 and the thick-walled roller sleeve 3 takes the tolerance H7 / v6.
[0034] The hot-packed thick-walled roll sleeve combination roll is safe and reliable during use, and its service life is twice as long as that of the original integral roll.
PUM
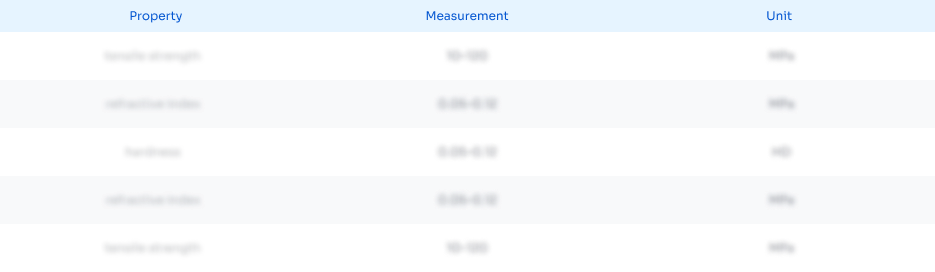
Abstract
Description
Claims
Application Information

- R&D Engineer
- R&D Manager
- IP Professional
- Industry Leading Data Capabilities
- Powerful AI technology
- Patent DNA Extraction
Browse by: Latest US Patents, China's latest patents, Technical Efficacy Thesaurus, Application Domain, Technology Topic, Popular Technical Reports.
© 2024 PatSnap. All rights reserved.Legal|Privacy policy|Modern Slavery Act Transparency Statement|Sitemap|About US| Contact US: help@patsnap.com