Manufacture technology of ball connection point with coreless necking bulging pressing method
A technology of preparation process and stamping method, which is applied to the production of ball joints by the coreless shrinking and bulging stamping method, and in the field of ball joint preparation and preparation for combined ball joint railings, which can solve the problems of many processes, many consumables, and increased costs. problems, to achieve the effect of improving safety performance, simple preparation process and high yield
- Summary
- Abstract
- Description
- Claims
- Application Information
AI Technical Summary
Problems solved by technology
Method used
Image
Examples
Embodiment 1
[0040] A ball joint for a combined ball joint railing and its preparation process, the preparation process is as follows:
[0041] Tubular blank→shrinking→bulging→shaping→hole repairing→stress relief heat treatment→inspection→warehousing;
[0042] Concrete preparation process steps and parameters are as follows:
[0043] (1) Preparation of blank:
[0044] The blank used in this preparation process is a tubular blank, which can be a forged tubular blank, a tubular blank processed by turning, or a tubular blank cut from a seamless tube; the size of the blank: L=1.57D-d k
[0045] D ball joint outer diameter
[0046] d k reserved hole diameter;
[0047] (2) necking
[0048] In this preparation process, the necking process is placed before the bulging process, and the necking is performed on the mold. The necking is multiple necking, the first necking, the necking coefficient is controlled at 0.8-0.9, and the necking coefficient is controlled by adjusting the The closed hei...
Embodiment 2
[0066] A ball joint for a combined ball joint railing and its preparation process, the preparation process is as follows:
[0067] Tubular blank→shrinking→bulging→shaping→hole repairing→stress relief heat treatment→inspection→warehousing;
[0068] Concrete preparation process steps and parameters are as follows:
[0069] (1) Preparation of blank:
[0070] The blank used in this preparation process is a tubular blank, which can be a forged tubular blank, a tubular blank processed by turning, or a tubular blank cut from a seamless tube; the size of the blank: L=1.57D-d k
[0071] D ball joint outer diameter
[0072] d k reserved hole diameter;
[0073] (2) necking
[0074] In this preparation process, the necking process is placed before the bulging process, and the necking is performed on the mold. The necking is multiple necking, the first necking, the necking coefficient is controlled at 0.8-0.9, and the necking coefficient is controlled by adjusting the The closed hei...
PUM
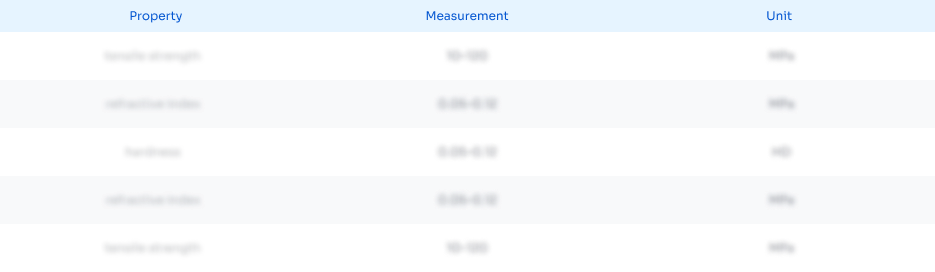
Abstract
Description
Claims
Application Information

- R&D Engineer
- R&D Manager
- IP Professional
- Industry Leading Data Capabilities
- Powerful AI technology
- Patent DNA Extraction
Browse by: Latest US Patents, China's latest patents, Technical Efficacy Thesaurus, Application Domain, Technology Topic, Popular Technical Reports.
© 2024 PatSnap. All rights reserved.Legal|Privacy policy|Modern Slavery Act Transparency Statement|Sitemap|About US| Contact US: help@patsnap.com