Process for internally heated continuous preparing biomass pyrolysis gasification gas and rotary furnace utilized by same
A technology for pyrolysis gasification and pyrolysis gas, which is applied in the fields of biofuels, manufacture of combustible gases, coke ovens, etc. It can solve the problems of affecting the quality of finished gas and occupying a large space, and achieve convenient operation, accurate control of material balance, and output. big effect
- Summary
- Abstract
- Description
- Claims
- Application Information
AI Technical Summary
Problems solved by technology
Method used
Image
Examples
Embodiment 1
[0035] A method for continuously preparing biomass pyrolysis gasification gas by internal heating, the steps are:
[0036] The biomass enters the furnace head preheating section of the pyrolysis gasification converter through the feed port, and the biomass is one or a mixture of wood blocks or fruit shells. The biomass moves from right to left in the furnace, and exchanges heat with the crude pyrolysis gas coming out of the pyrolysis section of the rotary furnace from left to right. After the biomass completes the drying and preheating process, the temperature of the crude pyrolysis gas after heat exchange After falling to 70°C, the crude pyrolysis gas is discharged from the outlet and enters the purification process for purification. Part of the purified gas is returned to the combustion device as returned gas to be mixed with air for combustion, and the heat generated is heated by the wall of the rotary inner cylinder through the flue. The biomass, the other part enters the ga...
Embodiment 2
[0045] A method for continuous pyrolysis and gasification of biomass converters. Firstly, wood blocks with a size of 50±30mm are sent into the pyrolysis and gasification rotary furnace, and they move from right to left in the furnace, and are pyrolyzed by the rotary furnace body. The crude pyrolysis gas coming out of the section from left to right is heat-exchanged. The wood blocks complete the drying and preheating process. After the heat exchange, the temperature of the crude pyrolysis gas drops to 70°C, and then it is discharged from the crude pyrolysis gas outlet for purification. The purified Part of the gas is returned to the combustion device 4 as returned gas to be mixed with air for combustion, and the heat generated passes through the flue 5 to heat the biomass in the rotating inner cylinder through the wall of the rotating inner cylinder, and the other part enters the gas cabinet for use;
[0046] After preheating and drying, the wood blocks enter the pyrolysis secti...
Embodiment 3
[0061] Such as figure 2 and 3 Shown, a kind of rotary kiln used in the method for the described internal heating type continuous preparation of biomass pyrolysis gasification gasification, described rotary kiln is from left to right by furnace head preheating section I, rotary kiln body pyrolysis Section II and furnace tail cooling section III are composed. The pyrolysis section II of the rotary furnace body is connected with the furnace head preheating section I and the furnace tail cooling section III through two supporting rollers at the front and rear.
[0062] A screw conveyor 2 is provided on the furnace head preheating section 1, and a raw material inlet is provided on the screw conveyor 2, and a crude pyrolysis gas outlet is provided on the furnace head preheating section;
[0063] The pyrolysis section II of the rotary furnace body is mainly composed of a rotary inner cylinder and an outer thermal insulation layer. A flue 5 is arranged between the rotary inner cylin...
PUM
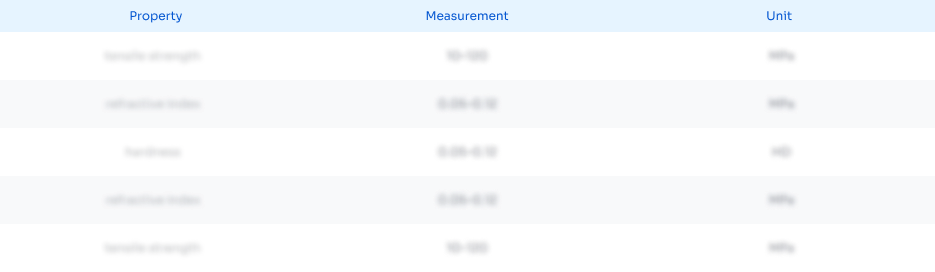
Abstract
Description
Claims
Application Information

- Generate Ideas
- Intellectual Property
- Life Sciences
- Materials
- Tech Scout
- Unparalleled Data Quality
- Higher Quality Content
- 60% Fewer Hallucinations
Browse by: Latest US Patents, China's latest patents, Technical Efficacy Thesaurus, Application Domain, Technology Topic, Popular Technical Reports.
© 2025 PatSnap. All rights reserved.Legal|Privacy policy|Modern Slavery Act Transparency Statement|Sitemap|About US| Contact US: help@patsnap.com