Efficient energy-saving process for continuously processing dihydromyrcenol
A technology for dihydromyrcenol and dihydromyrcene, which is applied in the field of continuous production of dihydromyrcenol, can solve the problems of high production cost, long reaction time, complicated operation, etc., and achieves reduction of equipment material and replacement process. Continuous, continuous and stable operation
- Summary
- Abstract
- Description
- Claims
- Application Information
AI Technical Summary
Problems solved by technology
Method used
Image
Examples
Embodiment 1
[0026] Dihydromyrcene, water and acetone solvent are 1: 1: 1 by mass ratio, reach 110 ℃ of reaction temperature through preheater 1, 2 and 3 respectively preheating, the pressure of strengthening jet reaction device 5 is 0.5MPa (gauge pressure ), and in the catalyst feeding device 4, enter into the strengthening spray reaction device 5 after mixing with the catalyst strong acid ion exchange resin Amberlyst 15 (produced by Rohm and Haas Company in the U.S.) (catalyst amount accounts for 10% of the material gross mass including solvent) . The material in the enhanced injection reaction device 5 enters the centrifugal pump 9 through the filter 17, passes through the heat exchanger 11, and is injected into the enhanced injection reaction device 5 by the injector 8 (the injector is provided by Shuanghong Engineering Technology Development Co., Ltd., the same below.) Inside. After the reaction was carried out for 3 hours, the valve 27 was opened to start discharging, and the materi...
Embodiment 2
[0028]Dihydromyrcene and water are 1: 1 by mass ratio, reach 105 ℃ of reaction temperature through preheater 1 and 2 respectively preheating, the pressure of strengthening injection reaction device 5 is 0.1MPa (gauge pressure), and in catalyst feeding device 4 enters into the enhanced injection reaction device 5 after being mixed with the catalyst strong acidic ion exchange resin Amberlyst 35 (produced by Rohm and Haas Company of the United States) (the amount of catalyst accounts for 12% of the total mass of the material). The reaction material in the enhanced injection reaction device 5 enters the centrifugal pump 9 through the filter 17 , passes through the heat exchanger 11 , and is sprayed into the enhanced injection reaction device 5 by the injector 8 . After the reaction was carried out for 3 hours, the valve 27 was opened, and the reactor began to discharge the material, which entered the phase separator 7. At the same time, the reaction material dihydromyrcene and wat...
Embodiment 3
[0030] Similar to the operation method of Example 1, dihydromyrcene, water and alcoholic solvent (ethanol, propanol or butanol) are 1: 1: 2 by mass ratio, and are preheated respectively through preheater 1, 2 and 3 to reach 115 ℃ of temperature of reaction, the pressure of strengthening spray reaction device 5 is 0.3MPa (gauge pressure), and in catalyst feeding device 4 and catalyst strongly acidic ion-exchange resin Amberlyst 36 (U.S. Rohm and Haas company production) (catalyst amount accounts for total 15% of the mass of the material) enters the enhanced injection reaction device 5 after being mixed. Other operating steps are the same as in Example 1. The conversion rate of dihydromyrcene in this hydration process is 99%, and the selectivity is more than 93%.
PUM
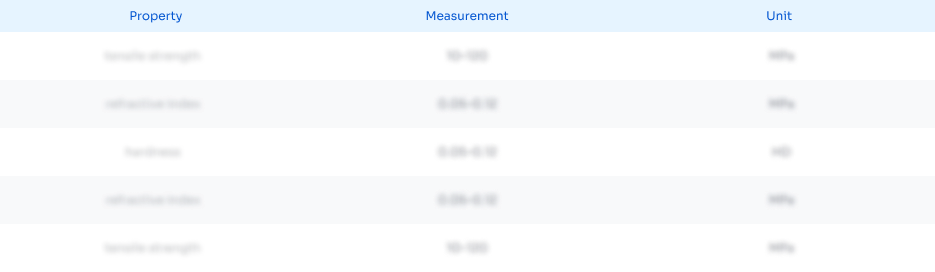
Abstract
Description
Claims
Application Information

- R&D Engineer
- R&D Manager
- IP Professional
- Industry Leading Data Capabilities
- Powerful AI technology
- Patent DNA Extraction
Browse by: Latest US Patents, China's latest patents, Technical Efficacy Thesaurus, Application Domain, Technology Topic, Popular Technical Reports.
© 2024 PatSnap. All rights reserved.Legal|Privacy policy|Modern Slavery Act Transparency Statement|Sitemap|About US| Contact US: help@patsnap.com