Sealing glass powder, sealing glass ceramic powder and application
A technology for sealing glass and ceramic powder, applied in the field of sealing glass ceramics, can solve the problems of deterioration of ceramic reinforced glass sealing material, inability to adapt to SOFC long-term operation, unreasonable glass composition, etc., and achieves stable thermal expansion coefficient, low cost, and use long life effect
- Summary
- Abstract
- Description
- Claims
- Application Information
AI Technical Summary
Problems solved by technology
Method used
Image
Examples
Embodiment 1
[0055] (1) With 25mol% SiO 2 , 22mol%B 2 o 3 , 20mol% BaO, 20mol% CaO, 6mol% MgO, 0.5mol% La 2 o 3 , 5mol% Y 2 o 3 , 1.5mol% ZrO 2 The ratio of each component was weighed, mixed evenly, and placed in a platinum crucible.
[0056] (2) Put the crucible with the raw material in the muffle furnace, keep it warm at 1300°C for 4 hours, cool it down to 800°C, take out the water quenching, make glass material, then crush the glass material into glass pieces, and crush the glass The lumps are ball-milled into a powder form, the particle size of the powder is 50-60 μm, and dried.
[0057] (3) Heat 7.5g of paraffin wax to 100°C, add 92g of glass powder, stir and mix, add 0.5g of oleic acid, and mix evenly to form a wax slurry.
[0058] (4) Inject the wax slurry into the mould, cool, and demould to obtain a glass blank.
[0059] (5) Heat the glass blank obtained in step (4) at 130°C for 0.5h to harden it.
[0060] (6) Place the hardened glass blank between the fuel cell connecti...
Embodiment 2
[0064] (1) With 25mol% SiO 2 , 22mol%B 2 o 3 , 20mol% BaO, 10mol% SrO, 10mol% CaO, 6mol% MgO, 0.5mol% La 2 o 3 , 5mol%Y 2 o 3 , 1.5mol% ZrO 2 The ratio of each component was weighed, mixed evenly, and placed in a platinum crucible.
[0065] (2) Put the crucible with the raw material in the muffle furnace, keep it warm at 1300°C for 3 hours, cool it down to 800°C, take out the water quenching, make glass material, and then crush the glass material into glass pieces. The block balls are ground into glass powder, the particle size of the glass powder is 90-100 μm, and dried.
[0066] (3) 80vol% glass powder, 10vol% MgO, 10vol% Y 2 o 3 Stable ZrO 2 The proportion of each component was weighed and mixed uniformly to obtain a glass ceramic powder.
[0067] (4) Heat 15.0 g of paraffin wax to 100° C., add 83.0 g of glass ceramic powder, stir and mix, add 1.0 g of oleic acid and 1.0 g of stearic acid, and mix evenly to form a wax slurry.
[0068] (5) Inject the wax slurry i...
Embodiment 3
[0074] (1) With 23mol% SiO 2 , 24mol%B 2 o 3 , 25mol% BaO, 15mol% CaO, 5mol% MgO, 1mol% La 2 o 3 , 5mol%Y 2 o 3 , 2mol% ZrO 2 The ratio of each component was weighed, mixed evenly, and placed in a platinum crucible.
[0075] (2) Put the crucible with the raw material in the muffle furnace, heat it at 1300°C for 5 hours, cool it down to 800°C, take out the water and quench it to make a glass material, and then crush the glass material into glass pieces. The block balls are ground into glass powder and dried.
[0076] (3) With 80vol% glass powder, 5vol% MgO, 5vol% ZrO 2 , 10vol% with Y 2 o 3 Stable ZrO 2 The proportion of each component was weighed and mixed uniformly to obtain a glass ceramic powder.
[0077] (4) Heat 10 g of paraffin wax to 80° C., add 88.5 g of glass ceramic powder, stir and mix, add 0.5 g of oleic acid and 1.0 g of stearic acid, and mix evenly to form a wax slurry.
[0078] (5) injecting the wax slurry into the mold, cooling, and demolding to ob...
PUM
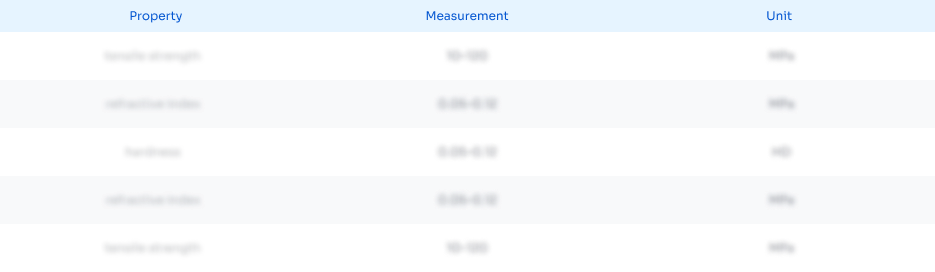
Abstract
Description
Claims
Application Information

- Generate Ideas
- Intellectual Property
- Life Sciences
- Materials
- Tech Scout
- Unparalleled Data Quality
- Higher Quality Content
- 60% Fewer Hallucinations
Browse by: Latest US Patents, China's latest patents, Technical Efficacy Thesaurus, Application Domain, Technology Topic, Popular Technical Reports.
© 2025 PatSnap. All rights reserved.Legal|Privacy policy|Modern Slavery Act Transparency Statement|Sitemap|About US| Contact US: help@patsnap.com