Composite binder for preparing sintered porous body of silicon carbide powder and using method thereof
A silicon carbide powder and binder technology, applied in the chemical field, can solve the problems of high strength, good high temperature resistance and low bonding strength of silicon carbide porous body, and achieve easy low temperature removal, good high temperature resistance, high the effect of strength
- Summary
- Abstract
- Description
- Claims
- Application Information
AI Technical Summary
Problems solved by technology
Method used
Examples
Embodiment 1
[0012] Dissolve aluminum hydroxide powder in 85% concentrated phosphoric acid at 140°C to obtain aluminum metaphosphate with a phosphorus-to-aluminum ratio of 23, add water and dilute to 5000 ml to obtain an aluminum metaphosphate solution with a concentration of 0.007 g / ml, add it to 7000 g In 10μm silicon carbide powder, stir evenly, dry at 200°C for 24 hours, pass through a 200 mesh sieve, add 1000 ml of polyvinyl alcohol aqueous solution with a concentration of 0.14 g / ml, grind evenly, dry at 80°C for 24 hours, and sieve (200 mesh), and then sintered at 800°C for 3 hours to obtain a silicon carbide porous body.
Embodiment 2
[0014] Dissolve aluminum hydroxide powder in 85% concentrated phosphoric acid at 140°C to obtain aluminum metaphosphate with a phosphorus-aluminum ratio of 23, add water and dilute to 5000 ml to obtain an aluminum metaphosphate solution with a concentration of 0.014 g / ml, add it to 7000 g In 10μm silicon carbide powder, stir evenly, dry at 200°C for 24 hours, pass through a 200 mesh sieve, add 1000 ml of polyvinyl alcohol aqueous solution with a concentration of 0.105 g / ml, grind evenly, dry at 80°C for 24 hours, and sieve (200 mesh), and then sintered at 800°C for 3 hours to obtain a silicon carbide porous body.
Embodiment 3
[0016] Dissolve aluminum hydroxide powder in 85% concentrated phosphoric acid at 140°C to obtain aluminum metaphosphate with a phosphorus-to-aluminum ratio of 23, add water and dilute to 5000 ml to obtain an aluminum metaphosphate solution with a concentration of 0.028 g / ml, add it to 7000 g In 10μm silicon carbide powder, stir evenly, dry at 200°C for 24 hours, pass through a 200 mesh sieve, add 1000 ml of polyvinyl alcohol aqueous solution with a concentration of 0.07 g / ml, grind evenly, dry at 80°C for 24 hours, and sieve (200 mesh), and then sintered at 800°C for 3 hours to obtain a silicon carbide porous body.
PUM
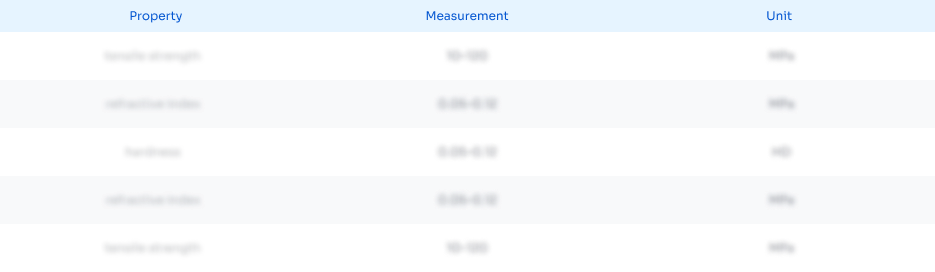
Abstract
Description
Claims
Application Information

- R&D
- Intellectual Property
- Life Sciences
- Materials
- Tech Scout
- Unparalleled Data Quality
- Higher Quality Content
- 60% Fewer Hallucinations
Browse by: Latest US Patents, China's latest patents, Technical Efficacy Thesaurus, Application Domain, Technology Topic, Popular Technical Reports.
© 2025 PatSnap. All rights reserved.Legal|Privacy policy|Modern Slavery Act Transparency Statement|Sitemap|About US| Contact US: help@patsnap.com