Thermal-mechanical coupling edge grinding technology applicable to manufacturing diamond tools
A diamond tool and sharpening technology, which is applied in the direction of manufacturing tools and other manufacturing equipment/tools, can solve the problems such as the sharpness of the edge of the diamond tool that cannot be solved, and achieve the effects of low cost, high efficiency and simple sharpening process.
- Summary
- Abstract
- Description
- Claims
- Application Information
AI Technical Summary
Problems solved by technology
Method used
Image
Examples
specific Embodiment approach 1
[0022] Specific implementation mode one: the step of a kind of thermal-mechanical coupling sharpening process that is suitable for the manufacture of diamond tool of this embodiment is:
[0023] Step 1: After the air vibration isolation pad is inflated, adjust the balance state of the sharpening machine to keep it level;
[0024] Step 2: The working surface of the steel grinding disc is heat-treated and finely polished after finishing turning, and the steel grinding working surface is controlled to achieve a mirror effect, and the hardness is HRC≥63, and then directly installed on the diamond tool sharpening machine without coating Diamond abrasive grains;
[0025] Step 3: Use a high-precision dynamic balancer to finely balance the spindle system of the grinding machine tool at a speed of 2800r / min, and control the radial rotation accuracy of the spindle to be less than 0.05μm and the axial rotation accuracy to be less than 0.1μm at a working speed of 2800r / min;
[0026] Step...
specific Embodiment approach 2
[0028]Specific implementation mode two: this implementation mode combines figure 1 The processing method of diamond tools is introduced in detail:
[0029] First, the thermal-mechanical coupling sharpening process system for diamond tools in this embodiment consists of an air vibration isolation pad 1, a cast iron bed 2, a printing motor 3, an air static pressure spindle 4, a tool clamping system 5, a counterweight 6 and Composed of steel grinding discs 8, air vibration isolation pads 1 are evenly distributed on the bottom of the cast iron bed 2, the lower part of the air static pressure spindle 4 is seated inside the cast iron bed 2, and the upper end of the air static pressure spindle 4 is connected with a steel grinding disc 8 , the end of the air static pressure main shaft 4 is connected with the output shaft of the printing motor 3, the top of the steel grinding disc 8 is equipped with a tool clamping system 5, and a counterweight 6 is placed on the tool clamping system 5...
PUM
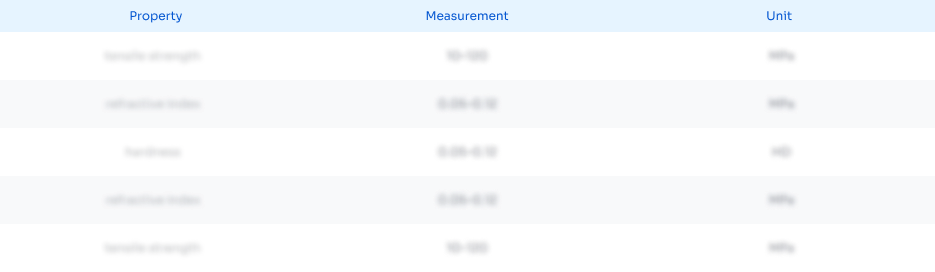
Abstract
Description
Claims
Application Information

- R&D
- Intellectual Property
- Life Sciences
- Materials
- Tech Scout
- Unparalleled Data Quality
- Higher Quality Content
- 60% Fewer Hallucinations
Browse by: Latest US Patents, China's latest patents, Technical Efficacy Thesaurus, Application Domain, Technology Topic, Popular Technical Reports.
© 2025 PatSnap. All rights reserved.Legal|Privacy policy|Modern Slavery Act Transparency Statement|Sitemap|About US| Contact US: help@patsnap.com