Zn-Mg magnesium alloy solder
A technology of magnesium alloy and brazing material, which is applied in the direction of welding/cutting medium/material, welding medium, welding equipment, etc., can solve the problems of high cost of brazing filler metal, increase the cost of brazing filler metal, etc., and achieve avoidance of oxidation and over-burning, and good spreading Sexual and gap-filling effects
- Summary
- Abstract
- Description
- Claims
- Application Information
AI Technical Summary
Problems solved by technology
Method used
Image
Examples
Embodiment 1
[0012] The chemical composition and mass percentage of the solder are: Mg: 4.0%, and the balance is Zn. The solder alloy is smelted by the flux protection method, poured into ingots, and then the solder is divided into strips and blocks by mechanical division. Before brazing, the AZ31B magnesium alloy sample was sanded and cleaned with acetone to remove surface dirt. The solder was placed at the joint, and the flux was evenly spread on the joint and the solder. The joint was fixed by a clamp and placed in an argon protection device for High frequency induction brazing. During the brazing process, the argon flow rate was 0.3L / min, the heating rate was 300°C / min, and the brazing temperature range was 420-450°C. After holding for 120s, cool to room temperature. After brazing, the appearance of the joint was well formed, and the shear strength and tensile strength of the brazed joint were measured, and the results are shown in Table 1.
Embodiment 2
[0014] The chemical composition and mass percentage of the solder are: Mg: 6.0%, and the balance is Zn. The solder alloy is smelted by the flux protection method, poured into ingots, and then the solder is divided into strips and blocks by mechanical division. Before brazing, the AZ31B magnesium alloy sample was sanded and cleaned with acetone to remove surface dirt. The solder was placed at the joint, and the flux was evenly spread on the joint and the solder. The joint was fixed by a clamp and placed in an argon protection device for High frequency induction brazing. During the brazing process, the argon gas flow rate was 0.3L / min, the heating rate was 300°C / min, and the brazing temperature range was 420-450°C. After holding for 120s, cool to room temperature. After brazing, the appearance of the joint was well formed, and the shear strength and tensile strength of the brazed joint were measured, and the results are shown in Table 1.
Embodiment 3
[0016] The chemical composition and mass percentage of the solder are: Mg: 8.0%, and the balance is Zn. The solder alloy is smelted by the flux protection method, poured into ingots, and then the solder is divided into strips and blocks by mechanical division. Before brazing, the AZ31B magnesium alloy sample was sanded and cleaned with acetone to remove surface dirt. The solder was placed at the joint, and the flux was evenly spread on the joint and the solder. The joint was fixed by a clamp and placed in an argon protection device for High frequency induction brazing. During the brazing process, the argon gas flow rate was 0.3L / min, the heating rate was 300°C / min, and the brazing temperature range was 420-450°C. After holding for 120s, cool to room temperature. After brazing, the appearance of the joint was well formed, and the shear strength and tensile strength of the brazed joint were measured, and the results are shown in Table 1.
[0017]
[0018] Chemical compositi...
PUM
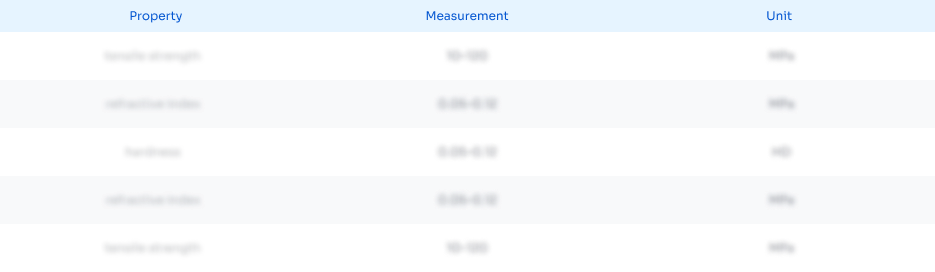
Abstract
Description
Claims
Application Information

- R&D
- Intellectual Property
- Life Sciences
- Materials
- Tech Scout
- Unparalleled Data Quality
- Higher Quality Content
- 60% Fewer Hallucinations
Browse by: Latest US Patents, China's latest patents, Technical Efficacy Thesaurus, Application Domain, Technology Topic, Popular Technical Reports.
© 2025 PatSnap. All rights reserved.Legal|Privacy policy|Modern Slavery Act Transparency Statement|Sitemap|About US| Contact US: help@patsnap.com