Process for corrosion-resistance passivation of ferrite stainless steel for packaging vehicle-mounted SCR
A passivation treatment, stainless steel technology, applied in the direction of metal material coating process, etc., can solve the problems of SCR system failure, inability to fully meet the chemical corrosion resistance requirements of vehicle-mounted SCR systems, vehicle failures and claims, etc., to improve life and significantly save money Benefits and social benefits, the effect of adding less
- Summary
- Abstract
- Description
- Claims
- Application Information
AI Technical Summary
Problems solved by technology
Method used
Image
Examples
Embodiment 1
[0021] The three-way catalytic converter (TWC) system in my country has high corrosion and failure problems. Corrosion condensate from the TWC system was analyzed and found to contain NH 4 + , CO 3 2- , PO 4 3- , SO 4 2- , Cl - , NO 3 - , organic acids and other highly corrosive condensates.
[0022] Prepare the corrosive medium according to the proportion in Table 1, put it into the hydrothermal reaction container respectively, put several stainless steel metal test pieces, reserve 50% of the volume space of the reaction container, close the reactor, put it into a constant temperature box, and put it in a constant temperature box at a temperature of 80 °C. , the temperature inside the reaction vessel can reach more than 100 ℃, which is a gas-liquid mixture. The composition of the corrosive medium to simulate the condensate prepared in the test is shown in Table 1.
[0023] Table 1 Composition of corrosive medium for simulated condensate
[0024]
[0025] * No...
Embodiment 2
[0032] a) Weigh distilled water in a corrosion-resistant container, heat it to 50°C, put in 4 parts of phosphoric acid, 0.05 part of nitric acid, and 0.5 part of acetic acid, and stir evenly;
[0033] b) adding 4 parts of aluminum dihydrogen phosphate with a content of 50% wt into a), stirring until completely dissolved;
[0034] c) adding 0.05 part of chromium nitrate and 0.005 part of zinc nitrate into b), stirring until completely dissolved; heating to make the temperature of the liquid reach 90 ° C;
[0035] A commercially available domestic ferritic stainless steel material, that is, a steel plate with a thickness of 1.5 mm, is first subjected to degreasing treatment, and then placed in the prepared passivation treatment solution c) at a temperature of 90°C for 12 minutes. Take out the passivated ferritic stainless steel material from the passivation solution c), wash with distilled water, and air dry to complete the chemical corrosion-resistant passivation treatment on t...
Embodiment 3
[0040] The samples of ferritic stainless steel 441 were first degreased and dried.
[0041]The passivation treatment liquid is as follows in the following proportions: 6 parts of phosphoric acid, 0.1 part of nitric acid, 0.5 part of acetic acid, 6 parts of 50% wt aluminum dihydrogen phosphate, 0.1 part of chromium nitrate, 0.01 part of zinc nitrate, and the remaining weights are distilled water, heated and stirred. , dissolve, complete the preparation. The ferritic stainless steel 441 sample was immersed and passivated in the above-mentioned passivation solution for 10 min at 95°C. Condensate corrosion medium was prepared according to the ratio of Table 1 of Example 1, and the passivation was completed according to the test conditions in Example 1. The treated ferritic stainless steel material was subjected to corrosion resistance test, and the results are shown in Table 4.
[0042] Table 4 Corrosion resistance test results of ferritic stainless steel 441 after passivation
...
PUM
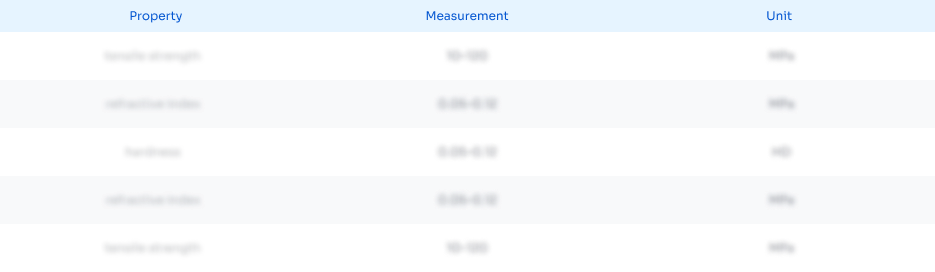
Abstract
Description
Claims
Application Information

- R&D
- Intellectual Property
- Life Sciences
- Materials
- Tech Scout
- Unparalleled Data Quality
- Higher Quality Content
- 60% Fewer Hallucinations
Browse by: Latest US Patents, China's latest patents, Technical Efficacy Thesaurus, Application Domain, Technology Topic, Popular Technical Reports.
© 2025 PatSnap. All rights reserved.Legal|Privacy policy|Modern Slavery Act Transparency Statement|Sitemap|About US| Contact US: help@patsnap.com