Production technology for preparing methanol by continuous oxidation of methane
A production process and methanol technology are applied in the production process field of methanol liquid-phase continuous oxidation of methane, which can solve the problems of providing design parameters and design basis for industrial production, inability to adjust, and high pressure, reducing the effective interface area and improving production efficiency. , the effect of stable production conditions
- Summary
- Abstract
- Description
- Claims
- Application Information
AI Technical Summary
Problems solved by technology
Method used
Image
Examples
Embodiment 1
[0038] The specific operation process is as above. The solvent is 50wt% oleum, in which elemental iodine is dissolved as a catalyst, and the methane gas and the catalyst-dissolved solvent are preheated to a reaction temperature of 200° C., a residence time of 25 min, and a reaction pressure of 4 MPa. When the ratio of the volume flow rate of methane to solvent is 200:1, and the mass ratio of solvent to catalyst is 1:0.005, the conversion rate of methane can reach 77% and the selectivity of methanol can reach 92%. The packing of the packing bubble column is Ф3 porcelain bowl packing, and the packing method is random packing.
[0039] The mass spectrogram of the dimethyl sulfate obtained by the rectification of the liquid phase product in the reaction process and the standard mass spectrogram of dimethyl sulfate, such as image 3 as shown, image 3 The first spectrum in the figure is the mass spectrum of the experimental measurement of dimethyl sulfate, and the second is the s...
Embodiment 2
[0041] The specific operation process is as above. The solvent is 50wt% oleum in which elemental iodine is dissolved as a catalyst, and the methane gas and the catalyst-dissolved solvent are preheated to a reaction temperature of 180° C., a residence time of 10 min, and a reaction pressure of 2 MPa. When the ratio of the volume flow rate of methane to solvent is 300:1, and the mass ratio of solvent to catalyst is 1:0.0005, the conversion rate of methane can reach 70% and the selectivity of methanol can reach 93% through measurement and calculation. The packing of the packing bubble column is Ф3 porcelain bowl packing, and the packing method is random packing.
Embodiment 3
[0043] The specific operation process is as above. The solvent is 50wt% oleum, in which sodium iodide is dissolved as a catalyst, and the methane gas and the catalyst-dissolved solvent are preheated to a reaction temperature of 160° C., a residence time of 20 min, and a reaction pressure of 1 MPa. When the volume flow rate ratio of methane to solvent is 100:1, and the mass ratio of solvent to catalyst is 1:0.01, the conversion rate of methane can reach 60% and the selectivity of methanol can reach 93.8%. The packing of the packed bubble column is Ф3 ceramic ring packing, and the packing method is regular packing.
PUM
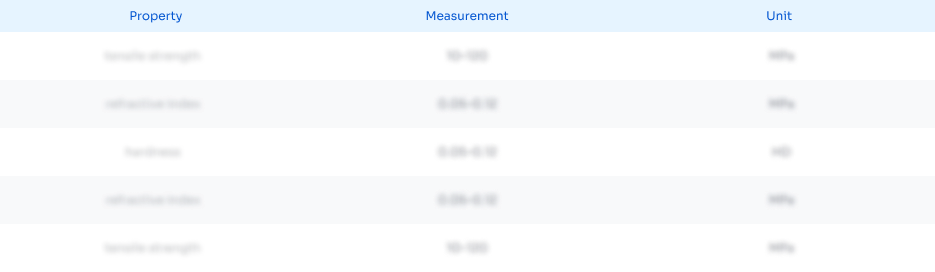
Abstract
Description
Claims
Application Information

- R&D
- Intellectual Property
- Life Sciences
- Materials
- Tech Scout
- Unparalleled Data Quality
- Higher Quality Content
- 60% Fewer Hallucinations
Browse by: Latest US Patents, China's latest patents, Technical Efficacy Thesaurus, Application Domain, Technology Topic, Popular Technical Reports.
© 2025 PatSnap. All rights reserved.Legal|Privacy policy|Modern Slavery Act Transparency Statement|Sitemap|About US| Contact US: help@patsnap.com