Process and device for preparing nano-powder by utilizing ultrasonic static electricity
A nano-powder and electrostatic technology, which is applied in the field of nano-powder preparation devices, can solve the problems of difficult complementarity of process shortcomings and inability to obtain cost-effectiveness, and achieve the effects of less agglomeration, good sphericity and uniform particle distribution.
- Summary
- Abstract
- Description
- Claims
- Application Information
AI Technical Summary
Problems solved by technology
Method used
Image
Examples
Embodiment 1
[0027] Preparation process of metal and alloy nanoparticles
[0028]The metal and alloy raw materials are first melted into a liquid state by the melting furnace, and then enter the degassing equipment for degassing. The degassed liquid raw material is charged by the pre-charger and then guided into the atomizer by the guide tube (the control of the charge of the raw material is achieved by controlling the voltage and current of the external DC power supply of the pre-charger), and then the ultrasonic After the nozzle system is atomized into droplets, it is accelerated by the acceleration ring group and enters the induction charging area formed by the induction charging ring for charging (the vibration frequency of the ultrasonic nozzle system is controlled by adjusting the parameters of the ultrasonic nozzle system power supply to achieve the control of the fog after the first atomization. Droplet diameter;. After charging, the charged droplets reach the Rayleigh limit for fu...
Embodiment 2
[0030] Preparation process of oxide nanoparticles
[0031] The prepared Cu(NO 3 ) 2 The solution is injected into the pre-charger for pre-charge treatment, and then guided into the ultrasonic nozzle system through the guide tube for atomization. Cu(NO 3 ) 2 The solution is accelerated into the inductive charging area formed by the inductive charging ring through the accelerating ring group for charging. After charging, the charged droplets reach the Rayleigh limit for further atomization, and the nanometer-scale droplets formed after atomization are accelerated by the acceleration ring group. After acceleration, the droplets are mixed by a "Y" tube and then irradiated by an alpha ray source. Remove surface charges. The surface charge-removed droplets then enter the thermal decomposition zone above the deflector, where Cu(NO 3 ) 2 The nanometer-scale droplets of the solution are heated and decomposed in the thermal decomposition zone to form copper oxide and NO 2 , O 2...
Embodiment 3
[0033] Composite particle preparation process
[0034] The main difference between the preparation of composite particles and the above two preparation processes is that the nano-scale droplets are recombined when they pass through the "Y" tube. When preparing composite particles, change the polarity of the two groups of pre-charged electrical appliances and induction charging rings of the atomizer to make them opposite. When the nano-scale droplets with different polarities converge through the "Y" tube, the droplets with different polarities have mutual attraction, and the nano-scale droplets with different polarities condense to form composite particles. Then dry (evaporate) and condense in the same condenser to generate solid powder.
PUM
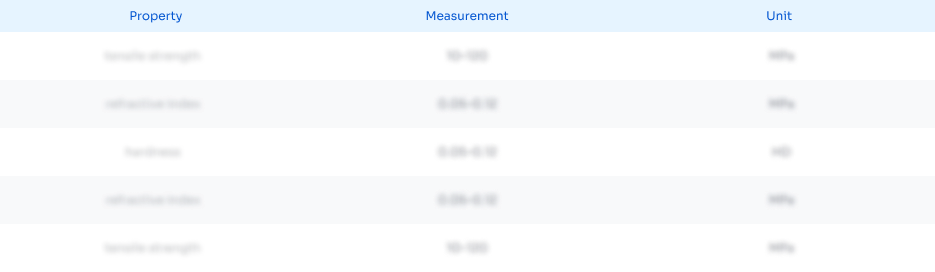
Abstract
Description
Claims
Application Information

- Generate Ideas
- Intellectual Property
- Life Sciences
- Materials
- Tech Scout
- Unparalleled Data Quality
- Higher Quality Content
- 60% Fewer Hallucinations
Browse by: Latest US Patents, China's latest patents, Technical Efficacy Thesaurus, Application Domain, Technology Topic, Popular Technical Reports.
© 2025 PatSnap. All rights reserved.Legal|Privacy policy|Modern Slavery Act Transparency Statement|Sitemap|About US| Contact US: help@patsnap.com