Flexible composite beam electric heating microdriver based on U+V shape
A technology of micro-driver and composite beam, which is applied in the direction of thermal effect motor, optical waveguide coupling, piezoelectric effect/electrostrictive or magnetostrictive motor, etc., which can solve the problem of low energy utilization rate, poor bonding force, thermal energy, etc. Large loss and other problems, to achieve the effect of improving energy utilization, preventing device failure, and easy process realization
- Summary
- Abstract
- Description
- Claims
- Application Information
AI Technical Summary
Problems solved by technology
Method used
Image
Examples
Embodiment Construction
[0025] The embodiments of the present invention are described in detail below. This embodiment is implemented on the premise of the technical solution of the present invention, and detailed implementation methods and specific operating procedures are provided, but the protection scope of the present invention is not limited to the following implementation example.
[0026] Such as Figure 1 to Figure 4 As shown, embodiment 1 includes: U-shaped beam base 1, U-shaped beam electrode 2, V-shaped beam base 3, V-shaped beam electrode 4, U-shaped double heating arm composite beam electrothermal driver 5 and V-shaped composite beam electrothermal driver The driver 6, wherein: two sets of U-shaped beam bases 1 and V-shaped beam bases 3 of the same structure are respectively located on the substrate, U-shaped beam electrodes 2 are located on the U-shaped beam base 1, and V-shaped beam electrodes 4 are located on the On the V-shaped beam base 3, the U-shaped double-arm composite beam el...
PUM
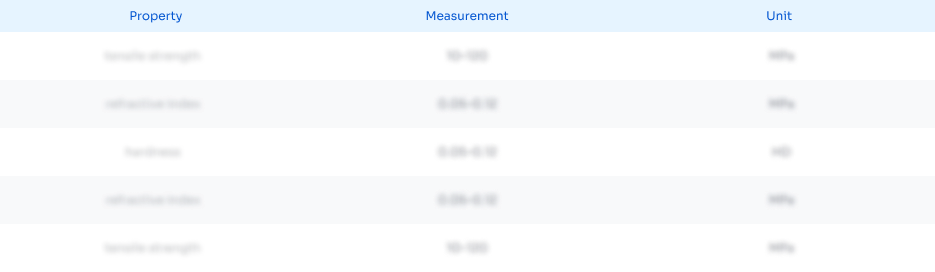
Abstract
Description
Claims
Application Information

- R&D Engineer
- R&D Manager
- IP Professional
- Industry Leading Data Capabilities
- Powerful AI technology
- Patent DNA Extraction
Browse by: Latest US Patents, China's latest patents, Technical Efficacy Thesaurus, Application Domain, Technology Topic, Popular Technical Reports.
© 2024 PatSnap. All rights reserved.Legal|Privacy policy|Modern Slavery Act Transparency Statement|Sitemap|About US| Contact US: help@patsnap.com